Steps in Sand Casting A Comprehensive Overview
Sand casting is a widely utilized metal casting process that allows for the production of intricate shapes and parts with high accuracy and excellent surface finishes. Commonly used for both ferrous and non-ferrous metals, this method is favored for its adaptability and relatively low cost. The steps involved in sand casting are essential to understanding how to produce high-quality castings effectively. In this article, we will explore each step in detail.
1. Pattern Making The first step in the sand casting process involves creating a pattern, which serves as a replica of the final product. Patterns can be made from various materials, including wood, metal, or plastic. The pattern is typically larger than the finished part because metal shrinks as it cools. Precision in pattern making is critical, as any inaccuracies will be transferred to the casting.
2. Preparing the Molding Box Once the pattern is completed, it is placed in a molding box, which consists of two halves the cope (top) and the drag (bottom). Sand mixed with a binding agent is packed around the pattern to form a mold. The composition of the sand and its moisture content are carefully controlled to ensure the best possible strength and flexibility.
Steps in Sand Casting A Comprehensive Overview
4. Removing the Pattern After the sand is adequately compacted, the pattern is removed carefully, leaving a cavity that matches the desired shape of the final product. This process requires skill to ensure that the mold is not damaged, as imperfections can affect the casting quality.
steps in sand casting
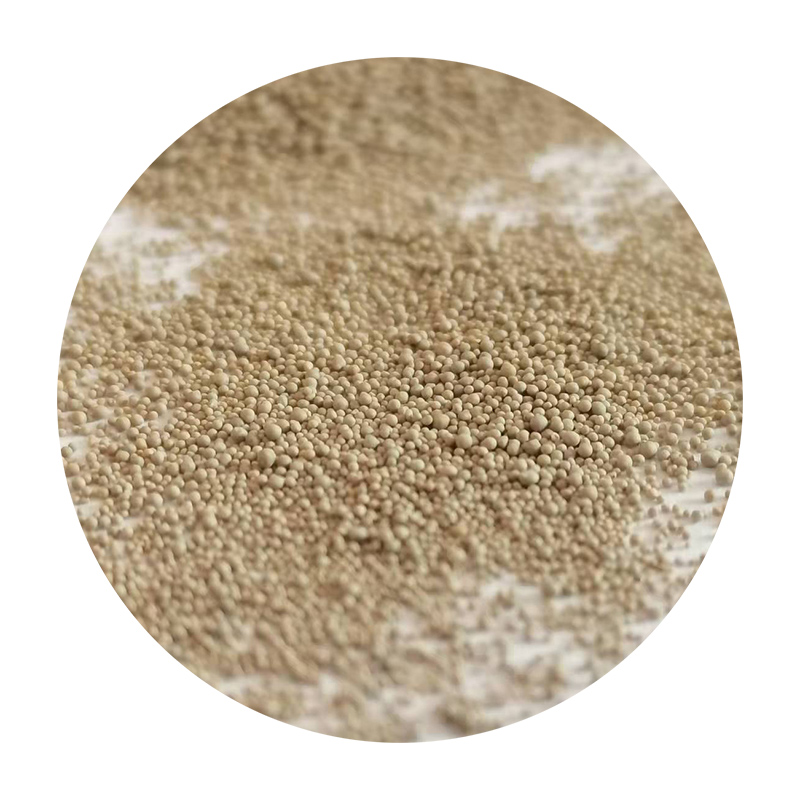
5. Adding the Pouring System To facilitate the molten metal's entry into the mold, a pouring system is designed. This typically includes a sprue, risers, and runners. The sprue acts as the main channel through which the metal enters, while risers and runners help control the flow and ensure complete filling of the mold.
6. Pouring the Metal With the mold prepared, the molten metal is poured into the mold cavity through the sprue. The pouring process must be executed carefully to prevent defects, such as turbulence and oxidation. The temperature of the molten metal must also be monitored to achieve the desired mechanical properties.
7. Cooling and Solidification Once the mold is filled, the metal is left to cool and solidify. The cooling time will vary based on the metal type and the thickness of the casting. It is crucial to allow adequate time for cooling to prevent cracking and warping.
8. Breakout and Finishing After the metal has cooled, the sand mold is broken apart to reveal the casting. The casting may require further finishing processes, such as machining, grinding, or surface treatment, to achieve the desired final specifications and surface finish.
In conclusion, sand casting is a versatile and cost-effective manufacturing process that involves several well-defined steps. By mastering these steps, manufacturers can produce high-quality castings that meet diverse industrial needs.
Post time:ኅዳር . 04, 2024 02:31
Next:sand casting definition