The Art of Sanding a 3D Print A Step-by-Step Guide
In the world of 3D printing, the excitement of creating a custom object often comes with the realization that post-processing is essential to achieve a polished final product. One of the most effective methods for enhancing the surface quality of your 3D prints is sanding. This article delves into the art of sanding a 3D print, providing a comprehensive guide to ensure your prints not only look good but feel good too.
Why Sand Your 3D Prints?
Sanding is a crucial step in post-processing that helps eliminate layer lines, which are a common characteristic of 3D printed objects. Layer lines can detract from the overall aesthetic and functionality of a print, especially for designs that require a smooth surface. Additionally, sanding can prepare a print for painting or further finishing processes, ensuring that the final product has a professional look.
Tools and Materials Needed
Before you start sanding, gather the necessary tools and materials
1. Sanding Sponge or Block A sanding sponge is flexible and can conform to the shape of your print, making it ideal for curved surfaces. 2. Sandpaper Use a range of grits, starting from coarse (around 60-80 grit) for aggressive material removal, and progressively moving to finer grits (up to 2000 grit) for a smooth finish. 3. Safety Gear Dust masks and goggles are essential to protect against fine particles generated during sanding. 4. Water or Alcohol Wet sanding can help reduce dust and improve the finish.
Step-by-Step Sanding Process
1. Prepare the Workspace Ensure you have a clean, well-ventilated area to work in. Lay down a drop cloth or old newspaper to catch debris.
sanding a 3d print
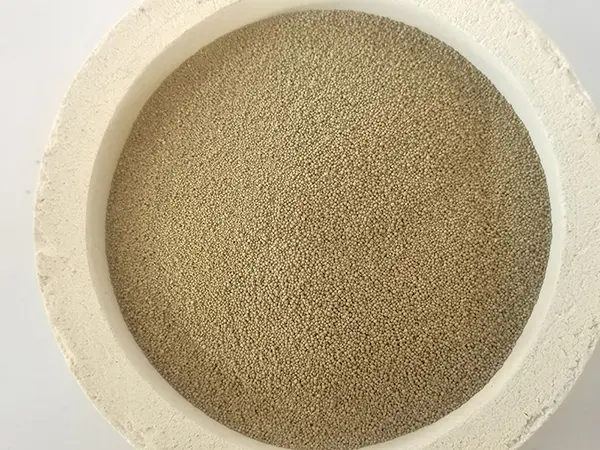
2. Inspect the Print Before sanding, examine the print closely for imperfections and identify areas that require attention. This assessment will guide your sanding process.
3. Start with Coarse Grit Begin with your coarse sandpaper (60-80 grit). Gently sand the surface using circular motions. Don’t apply too much pressure, as this can unintentionally alter the shape of your print.
4. Shift to Medium Grit Once you have smoothed out the roughest areas, switch to medium grit sandpaper (150-220 grit). Continue to sand in circular motions, gradually flattening the surface and minimizing layer lines.
5. Fine Detailing After achieving a smoother surface, move to finer grits (400-800 grit). This step is crucial for refining the finish. Again, use gentle pressure and continue working in circular motions.
6. Wet Sanding (Optional) If you want to achieve an even smoother finish, consider wet sanding with fine grit sandpaper (1000-2000 grit). Dampen the sandpaper with water or alcohol and sand the print lightly. This reduces dust and creates a finer surface.
7. Cleaning Up After sanding, clean your print with a soft cloth or brush to remove any dust particles. Inspect the result closely to determine if further sanding is necessary.
8. Final Touches If desired, apply a primer or paint to your print to enhance its appearance further. Remember to allow adequate drying time between coats.
Conclusion
Sanding a 3D print is a meticulous process that requires patience and attention to detail. The transformation from a rough, layered print to a smooth, visually appealing object can be incredibly satisfying. By following the steps outlined in this guide, enthusiasts can elevate their 3D printing projects and produce high-quality creations that stand out. Whether you are creating prototypes, models, or artistic pieces, mastering the art of sanding is an invaluable skill in the realm of 3D printing. So, grab your tools and get sanding—your perfect print awaits!
Post time:ታኅሣ . 04, 2024 20:31
Next:3d printed sand