Sand Casting Tolerances An Overview
Sand casting is a widely used manufacturing process that allows for the creation of complex metal components by pouring molten metal into a sand mold. This method is particularly popular for its versatility and cost-effectiveness, making it an ideal choice for producing both small and large quantities of cast parts. Understanding the tolerances associated with sand casting is crucial for engineers and manufacturers, as it can significantly influence the final quality and functionality of the products.
What Are Tolerances in Sand Casting?
Tolerances refer to the permissible limits of variation in a manufactured part. In sand casting, tolerances are especially important because they directly impact factors such as fit, assembly, and performance of the final components. These tolerances can encompass dimensional accuracy, surface finish, and other specific features necessary for the functionality of the part.
Factors Influencing Sand Casting Tolerances
Several factors affect the tolerances achievable through the sand casting process
1. Pattern Design The initial design of the pattern plays a critical role in determining tolerances. Patterns are typically slightly oversized to account for metal shrinkage during cooling. The precision of the pattern design can either enhance or detract from the final tolerance of the cast part.
2. Mold Material The type of sand and resin used in creating the mold can also influence tolerances. High-quality sand with a suitable grain size and uniformity can produce smoother surfaces and better dimensional accuracy.
sand casting tolerances
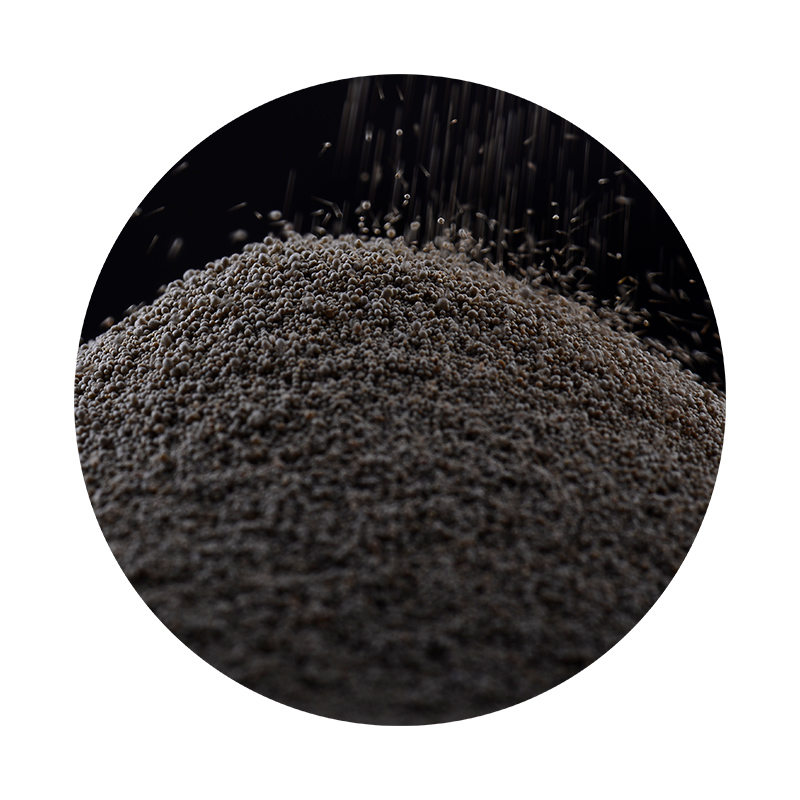
3. Pouring Temperature The temperature of the molten metal when poured into the mold affects how the metal flows and fills the mold. Maintaining an optimal pouring temperature is essential to prevent defects like cold shuts or misruns, which can compromise dimensions.
4. Cooling Rate The cooling process can lead to shrinkage in the final product. Controlled cooling rates can help minimize this shrinkage, leading to parts that meet tighter tolerances.
5. Post-Casting Processes Additional machining or finishing processes can be utilized to achieve the required tolerances if they cannot be achieved through casting alone. However, it’s essential to balance the cost and time implications of these secondary operations.
Standard Tolerances for Sand Casting
While tolerances can vary based on specific applications and requirements, industry standards provide guidelines for commonly accepted tolerances in sand casting. Generally, linear tolerances can range from ±0.5% to ±1% of the overall dimensions for most cast parts. For intricate shapes or critical applications, tighter tolerances may be necessary and can stretch up to ±0.3%.
Surface finish is another critical aspect, often measured using roughness average (Ra). Conventional sand cast surfaces can range from Ra 3.2 to Ra 12.5 micrometers, but specialized treatments can improve this significantly.
Conclusion
Understanding sand casting tolerances is vital for anyone involved in the design and manufacturing of cast parts. By considering factors such as pattern design, mold material, pouring temperature, and post-casting processes, manufacturers can optimize tolerances to ensure the components meet the necessary specifications. As technology continues to advance, innovations in sand casting processes may further enhance the precision and quality achievable in casting operations, leading to better performance and increased reliability of metal components in various applications. Balancing design intent with manufacturing capabilities will ultimately determine the success and efficiency of the sand casting process.
Post time:ታኅሣ . 13, 2024 19:38
Next:when was sand casting invented