The Comprehensive Guide to Sand Castings Manufacturing
Sand casting is one of the oldest and most widely used manufacturing processes for producing metal parts and components. It involves pouring molten metal into a sand mold to form intricate shapes and designs, making it an ideal choice for both large-scale production and small-batch runs. This article will explore the nuances of sand casting, its advantages, and how manufacturers can excel in this dynamic field.
Understanding Sand Casting
At its core, sand casting involves creating a mold from a mixture of sand and a binding agent. The process begins by creating a pattern, usually made from metal, plastic, or wood, which replicates the final product. This pattern is placed in a sand mixture, and when the sand is compacted around it, it forms a mold cavity. Once the mold is prepared, molten metal is poured into this cavity and allowed to cool and solidify.
Advantages of Sand Casting
1. Versatility Sand casting can be used for a wide variety of metals, including aluminum, bronze, brass, and cast iron. This versatility allows manufacturers to cater to diverse industries, from automotive to aerospace.
2. Complex Shapes The flexibility of sand molds enables the production of complex geometries that may be challenging for other manufacturing processes. This capability opens the door to innovative designs that meet specific functional requirements.
3. Cost-Effectiveness Sand casting is relatively inexpensive compared to other methods like die casting. The raw materials—sand and metal—are readily available, and the initial tooling costs for producing patterns can be amortized over large production runs.
4. Size Range From small components to large industrial parts weighing several tons, sand casting can accommodate a broad spectrum of sizes. This feature is remarkably beneficial for manufacturers serving specialized markets.
The Sand Casting Process
The sand casting process consists of several key steps
sand castings manufacturer
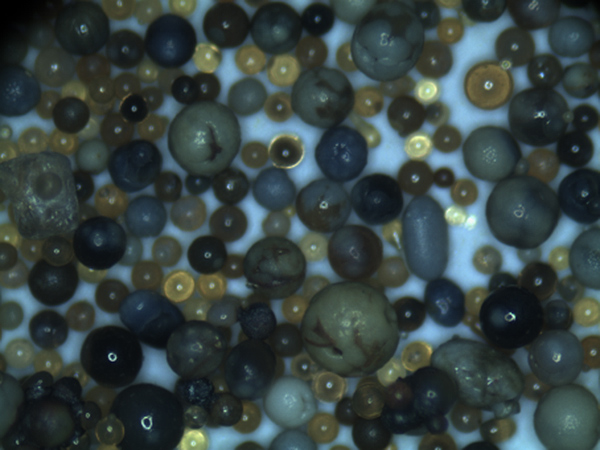
1. Pattern Making The first step involves creating a precise pattern that reflects the dimensions of the final product. This pattern must consider shrinkage and other factors during the cooling process.
2. Mold Preparation The pattern is embedded in a mixture of sand and a binding agent. The sand is compacted around the pattern to form the mold.
3. Metal Melting The selected metal is heated until it melts. The molten metal must reach optimal pouring temperatures to ensure proper flow and detail capture in the mold.
4. Pouring Once the metal is molten, it is carefully poured into the mold cavity. This step requires precision to avoid defects such as air pockets or incomplete filling.
5. Cooling After pouring, the metal is allowed to cool and solidify. The cooling time varies based on the metal type and the thickness of the casting.
6. Finishing Once the metal has cooled, the mold is broken away, revealing the casting. Finishing processes, including sanding, machining, and surface treatment, may be performed to achieve the desired final specifications.
Challenges in Sand Casting
Despite its many advantages, sand casting is not without challenges. Surface finish quality may not always meet high standards, and the dimensional tolerances can vary. Moreover, skillful handling and attention to detail are required during the pattern-making and pouring stages to minimize defects.
Conclusion
Sand casting remains a vital manufacturing method cherished for its adaptability and cost-effectiveness. It plays an essential role across various industries, providing fused metal parts that meet unique specifications. As manufacturers strive for precision and innovation, understanding the intricacies of sand casting will continue to be paramount to success in this dynamic field. By leveraging the strengths of sand casting and addressing its challenges, manufacturers can not only meet but exceed customer expectations, driving growth and sustainability in their operations.
Post time:ታኅሣ . 19, 2024 01:11
Next:Understanding the Principles and Advantages of Lost Foam Casting in Foundry Processes