Understanding Sand Casting Services A Comprehensive Overview
Sand casting, one of the oldest and most versatile metal casting processes, serves as a cornerstone in various manufacturing industries. Known for its simplicity and adaptability, sand casting utilizes a mixture of sand and binder to create molds that shape metals into specific forms. This article delves into the intricacies of sand casting services, exploring its advantages, applications, and the processes involved.
What is Sand Casting?
Sand casting is a method where a mold is formed from sand, creating a cavity that is subsequently filled with molten metal. The process begins with the creation of a pattern, which is a replica of the object to be cast. The pattern is typically made of metal, wood, or plastic. Once the pattern is in place, sand mixed with a binding agent is packed around it to form the mold. After the mixture has hardened, the pattern is removed, leaving a cavity that matches the desired shape. Finally, molten metal is poured into this cavity and allowed to cool, solidifying into the final product.
Advantages of Sand Casting
One of the primary advantages of sand casting is its cost-effectiveness. The materials used, particularly sand, are relatively inexpensive and readily available. Additionally, the sand can be reused multiple times, minimizing waste and reducing costs further. Sand casting is highly versatile, capable of producing parts of virtually any size—ranging from small intricate pieces to large, heavy components. Moreover, it lends itself to a wide variety of metals, including aluminum, iron, and bronze, making it suitable for diverse applications.
The process also permits a high level of customization. Foundries can easily modify patterns and molds to ensure that unique design specifications are met. This flexibility is invaluable in industries where customized components are essential, such as aerospace, automotive, and artistic applications.
Applications of Sand Casting
Sand casting is widely used across various sectors, owing to its flexibility and effectiveness. In the automotive industry, for instance, manufacturers rely on sand casting for engine blocks, transmission cases, and other crucial components. The aerospace sector uses sand casting to produce lightweight yet durable parts that can withstand high-stress conditions.
Moreover, the construction and shipbuilding industries utilize sand casting to create heavy-duty components such as valves, pumps, and structural elements. Even in artistic ventures, sand casting plays a role, allowing sculptors and designers to bring their creative visions to life, whether through sculptures or ornamental pieces.
sand casting services
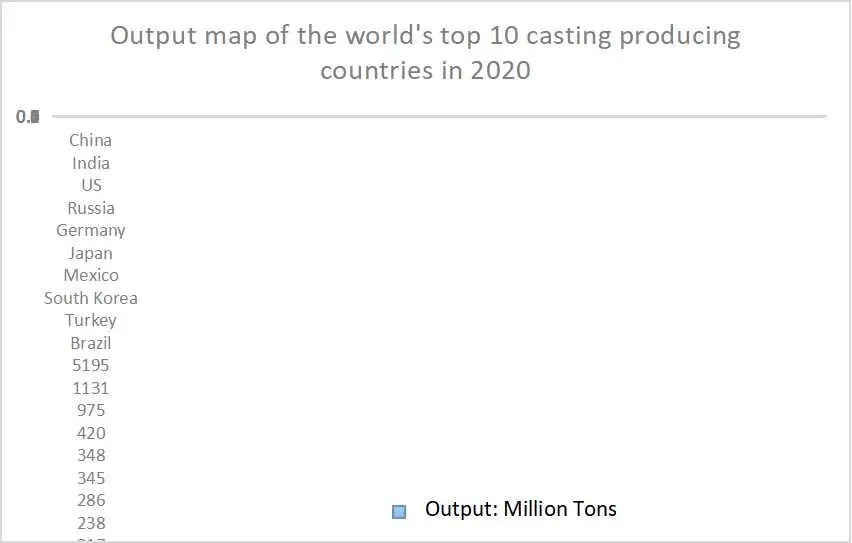
The Sand Casting Process
The sand casting process involves several key steps
1. Pattern Making Creating a precise replica of the object to be cast, with allowances for shrinkage and machining. 2. Mold Preparation The pattern is placed in sand mixed with a binder, creating a mold that captures the pattern’s details.
3. Core Making If the part requires hollow sections, sand cores are constructed to form these cavities.
4. Pouring Molten metal is poured into the mold, filling the cavity created by the pattern.
5. Cooling The metal is allowed to cool and solidify, taking the shape of the mold.
6. Mold Removal The sand mold is broken away to reveal the cast metal piece.
7. Finishing The cast part may undergo additional processes, such as grinding, machining, or surface finishing.
Conclusion
Sand casting services offer a reliable and cost-effective solution for producing a wide range of metal components. With its ability to accommodate intricate designs and large volumes, it remains a popular choice in many industries. As technology continues to advance, sand casting is likely to evolve, incorporating more innovative practices and materials, thus further enhancing its significance in the manufacturing landscape. Whether for industrial applications or artistic endeavors, sand casting remains an invaluable technique in the world of metalworking.
Post time:ኅዳር . 12, 2024 09:32
Next:sand casting technology