The Sand Casting Metal Process An Overview
Sand casting is one of the oldest and most versatile metalworking methods utilized in manufacturing. This widely adopted process is revered for its simplicity, cost-effectiveness, and ability to produce complex-shaped components. In this article, we'll explore the fundamentals of sand casting, its benefits, challenges, and the applications that underline its enduring relevance in modern industry.
What is Sand Casting?
At its core, sand casting involves creating a mold from sand, into which molten metal is poured to form a desired shape. The process begins with a pattern, typically made of metal or wood, which replicates the final product’s dimensions. This pattern is placed in a sand mixture that contains a binder. The sand is compacted around the pattern, creating a mold cavity. Once the mold is prepared, the pattern is removed, leaving a hollow form that represents the desired part.
After the mold is complete, molten metal—often aluminum, iron, or steel, depending on the required properties—is poured into the cavity. The metal fills the voids, taking the shape of the mold. After the metal solidifies, the mold is broken apart to reveal the cast part. The final step involves cleaning and finishing the component to meet specified tolerances.
Advantages of Sand Casting
One of the main advantages of sand casting is its flexibility. It can accommodate a wide range of metal types and can produce both small and large components, making it suitable for various industries, from automotive to aerospace. Furthermore, the process can produce complex geometries that might be challenging to achieve using other manufacturing methods, such as machining.
The cost-effective nature of sand casting is another contributing factor to its widespread use. The materials required for sand molds—silica sand and a binding agent—are relatively inexpensive and readily available. Additionally, the process allows for the efficient production of large volumes of parts, making it ideal for both low and high-volume applications.
sand casting metal process
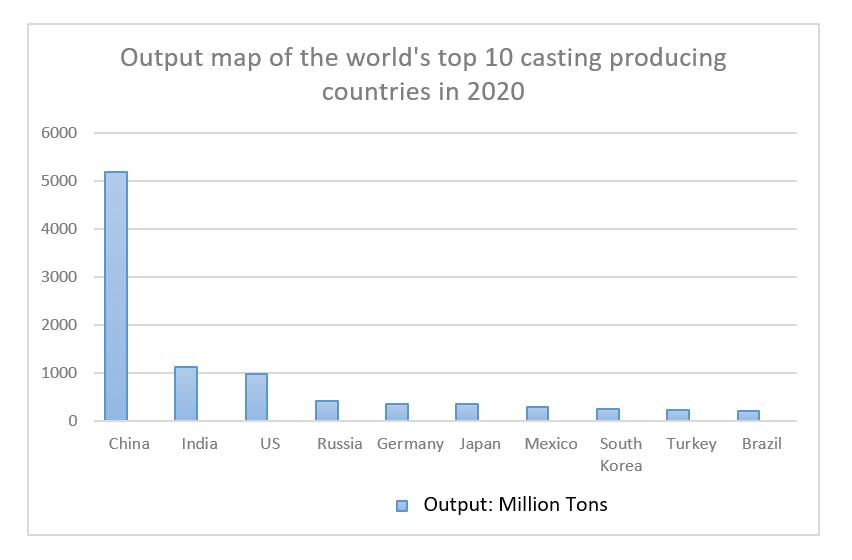
Challenges in Sand Casting
Despite its many benefits, sand casting does come with certain challenges. One notable issue is surface finish; parts produced via this method often require additional machining to achieve desirable surface qualities, which can add time and costs to the manufacturing process. Furthermore, the sand molds can be prone to variations caused by environmental factors, such as moisture levels, which can affect the final product's dimensions and quality.
Another challenge is the need for skilled labor to create and manage the process effectively. While the initial setup may be simple, the intricacies of ensuring that molds are correctly formed, poured, and finished require expertise and experience.
Applications of Sand Casting
The applications of sand casting are vast and varied. It is especially prevalent in the automotive industry for producing engine blocks, transmission housings, and other critical components. The aerospace sector also employs sand casting techniques for specific parts that demand high performance and precision.
Additionally, sand casting is frequently utilized in the manufacture of large industrial components, such as turbines and pumps. Its ability to produce complex shapes makes it an ideal choice for artistic applications, allowing for the creation of sculptures and intricate designs.
Conclusion
In conclusion, the sand casting metal process stands as a testament to the ingenuity of traditional manufacturing practices. Its ability to produce intricate shapes with diverse materials continues to play a vital role in various industries. While challenges exist, ongoing developments in materials science and manufacturing technology promise to enhance the capabilities and efficiencies of this ancient technique. As industries evolve, sand casting remains a crucial method in producing the components that drive our modern world, demonstrating a balance of tradition and innovation that keeps it relevant in today’s manufacturing landscape.
Post time:መስከ . 29, 2024 02:44
Next:Benefits of Sand Casting for Efficient Metal Fabrication and Production