Sand Casting Materials The Backbone of Foundry Processes
Sand casting, one of the oldest and most versatile manufacturing processes, relies heavily on the selection of appropriate materials to produce high-quality cast products. This technique involves pouring molten metal into a mold created from sand, which can take various forms depending on the desired final product. The materials used in sand casting play a crucial role in determining the efficiency, accuracy, and overall quality of the casting. This article will explore the primary materials involved in sand casting, their characteristics, and their significance in the casting process.
1. Sand
The most essential material in sand casting is, of course, the sand itself. Most commonly, silica sand is used due to its excellent properties, such as thermal stability, availability, and cost-effectiveness. Silica sand is made mostly of silicon dioxide (SiO2), and its grain size is crucial for creating detailed molds. Fine sand yields a smooth surface finish, while coarser sand provides better ventilation and strength to the mold.
Other types of sand, such as olivine sand, zircon sand, or chromite sand, may also be employed, particularly in applications requiring higher temperatures or specialized properties. The binder used with the sand is another critical factor; clay is often mixed with sand to enhance its cohesiveness and strength, allowing the mold to maintain its shape during casting.
2. Binders
Binders are materials that help hold the sand grains together, providing structural integrity to the mold. Traditionally, clay has been the most common binder used in sand casting. However, with advancements in technology, synthetic binders have gained popularity due to their superior performance and environmental benefits. Examples include phenolic resins, furan resins, and polyurethane binders that offer fast curing times and excellent dimensional stability.
Selecting the right binder is essential, as it can significantly affect the casting’s surface finish, dimensional accuracy, and overall strength
.3. Additives
sand casting materials
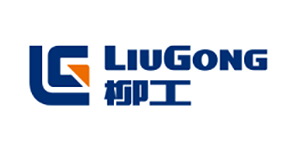
To enhance the properties of sand molds, various additives may be introduced. These can include materials that improve flowability, reduce moisture content, or increase thermal stability. Common additives are coal dust, which can enhance the surface finish, and various types of surfactants, which prevent sand from sticking to the mold.
4. Metal Alloys
The choice of metal alloy is a pivotal consideration in the sand casting process. Various materials can be used, including aluminum, iron, bronze, and magnesium alloys. Each type of alloy offers unique characteristics; for example, aluminum alloys are favored for their lightweight and corrosion resistance, while iron is appreciated for its strength and castability.
The selection of metal not only impacts the mechanical properties of the final product but also affects the casting process itself, including the temperature required for melting and the cooling rates.
5. Coatings
To prevent molten metal from adhering to the mold and to improve the surface finish of the cast, coatings are often applied to the mold before casting. These coatings can be made from various materials like graphite or ceramic compounds. They serve dual purposes enhancing the quality of the final product and prolonging the lifespan of the mold.
Conclusion
The materials used in sand casting are critical to the success and efficiency of the casting process. From the choice of sand and binders to the selection of metal alloys and coatings, each material plays a significant role in producing high-quality cast products. As technology continues to evolve, innovations in material science will further enhance the capabilities of sand casting, paving the way for more complex designs and better performance in various applications. Understanding these materials is essential for anyone involved in the foundry industry, ensuring that the final products meet demanding standards of quality and performance.
Post time:ኅዳር . 28, 2024 04:06
Next:The History and Evolution of Sand Casting Techniques Through the Ages