Sand Casting Manufacturing Process
Sand casting is a widely used manufacturing process known for its versatility and cost-effectiveness, particularly suited for producing complex metal components. This method leverages the unique properties of sand, which, when mixed with a binding agent, can create molds into which molten metal is poured. This article explores the sand casting process, its advantages, and its applications.
The Sand Casting Process
The sand casting process begins with the creation of a pattern, which is a replica of the desired part. Patterns can be made from various materials, including metal, wood, or plastic, depending on the size and complexity of the desired mold. Once the pattern is ready, it is used to create a mold in sand.
The sand used in casting is typically mixed with a binder to strengthen the mold. This mixture is packed around the pattern to form a mold cavity. The sand is then compacted to ensure that it holds its shape during the metal pouring stage. Once the mold is set, the pattern is removed, leaving behind a cavity in the shape of the desired component.
Next, the mold is assembled, often consisting of two halves. This assembly is crucial, as it ensures that the mold remains aligned during the metal pouring process. The assembled mold is then heated if necessary to prevent the molten metal from cooling too quickly, ensuring better surface finishes and dimensional accuracy.
With the mold prepared, molten metal is poured into the cavity. The choice of metal often depends on the application but commonly includes aluminum, iron, and bronze due to their favorable casting properties. The pouring must be done carefully to avoid introducing defects like air pockets or inclusions in the final piece.
sand casting manufacturing process
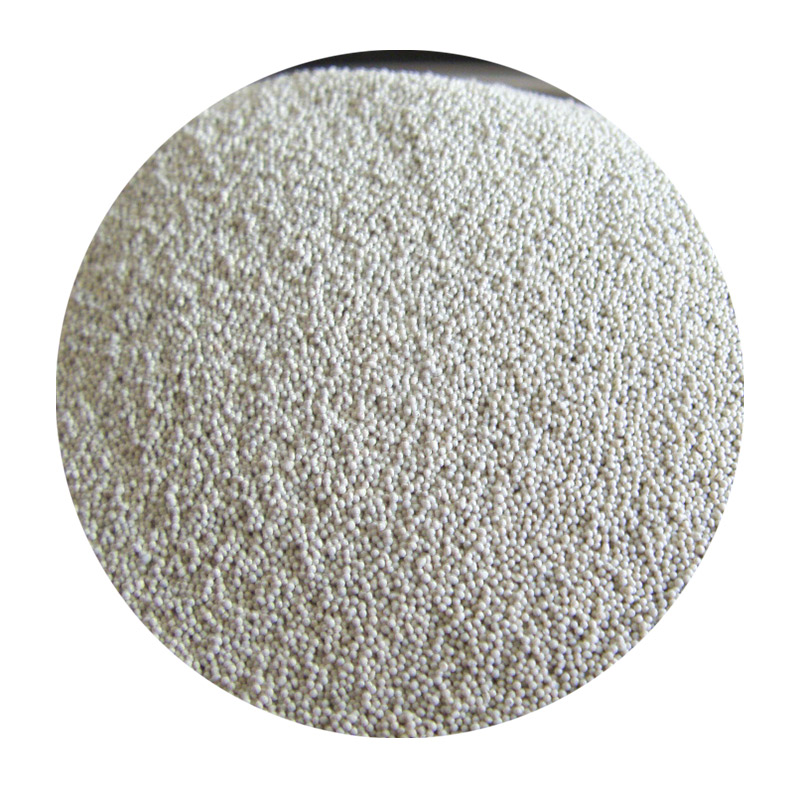
After the metal cools and solidifies, the mold is broken apart to extract the cast part. This phase may involve mechanical shaking or vibration to ensure that the sand mold crumbles away. Once the part is removed, any excess material from the casting process, known as flash, is trimmed off. Lastly, the component may undergo a series of finishing processes, such as machining, polishing, or surface treatments to enhance its properties.
Advantages of Sand Casting
One of the primary advantages of sand casting is its capability to produce large, complex shapes without the need for expensive tooling. This flexibility makes it an excellent choice for low to medium volume production runs. Additionally, the process allows for the use of multiple types of metals, providing designers and engineers with various material options to suit different applications.
Furthermore, sand casting has a relatively low setup cost compared to other casting methods, making it an attractive option for prototypes and unique components. The materials used, namely sand and binder, are readily available and recyclable, promoting environmentally friendly practices.
Applications
Sand casting is utilized across several industries, including automotive, aerospace, and general manufacturing. Its ability to create intricate components makes it ideal for producing engine blocks, gear housings, and other critical parts. The versatility of sand casting also extends to artistic applications, such as sculptures and decorative pieces.
In conclusion, the sand casting manufacturing process is a time-tested method that offers numerous advantages for creating complex metal parts. Its cost-effectiveness, flexibility, and efficiency make it a go-to choice for many industries, ensuring its continued relevance in modern manufacturing.
Post time:ጥቅም . 06, 2024 09:40
Next:rapid sand casting