Understanding the Sand Casting Process A Deep Dive into the Sand Casting Factory
Sand casting, also known as sand mold casting, is one of the oldest and most versatile metal casting processes. It involves the use of sand as the primary mold material to shape molten metal into desired forms. As a crucial component of the manufacturing industry, sand casting factories play a pivotal role in producing a vast array of metal components used in automobiles, machinery, and various other applications. This article will explore the intricacies of sand casting, the operations within a sand casting factory, and the benefits of this manufacturing method.
The Sand Casting Process
The sand casting process begins with the creation of a pattern, which is a model of the final product. This pattern is typically made from metal or plastic and is designed to be slightly larger than the finished part to account for metal shrinkage during cooling. Once the pattern is prepared, it is placed in a mold box, which is then filled with a mixture of sand and a binding agent such as clay.
After the sand is packed around the pattern, it is removed to create a hollow cavity in the shape of the part. The mold is then assembled, and molten metal is poured into the cavity. Once the metal cools and solidifies, the mold is broken apart, and the finished casting is removed. This method allows for a high degree of precision and is suitable for both small and large production runs.
Key Operations in a Sand Casting Factory
The operations in a sand casting factory are systematically organized to optimize efficiency and quality. Key stages include
2. Mold Preparation In this stage, the sand is mixed with the appropriate binder to form a mold. The mixture must be just right to ensure the mold holds its shape and can withstand the heat of the molten metal.
3. Casting This is where the molten metal is poured into the prepared mold. Depending on the material being cast, temperatures can exceed 1,000 degrees Celsius.
4. Cooling and Shakeout After pouring, the metal must cool and solidify, which can take varying amounts of time based on thickness. Once cooled, the mold is broken apart, and the casting is retrieved.
sand casting factory
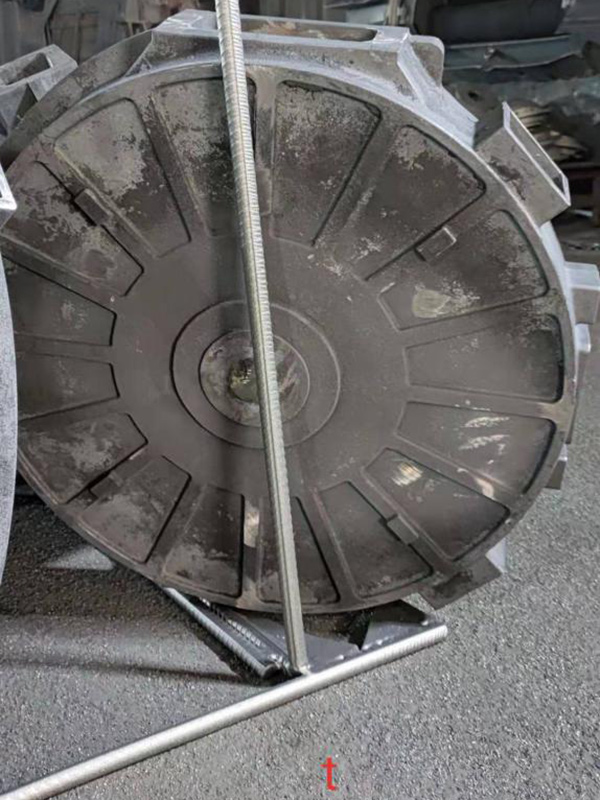
5. Finishing The castings often require additional processes such as sanding, machining, polishing, or painting to achieve the desired finish and specifications.
6. Quality Control Each step of the process includes quality control measures to ensure that the final product meets industry standards and customer requirements.
Advantages of Sand Casting
Sand casting offers numerous advantages that make it a preferred choice in many manufacturing scenarios
- Versatility Sand casting can accommodate a wide range of materials, including ferrous and non-ferrous metals, making it suitable for various applications.
- Cost-Effective Compared to other casting methods, sand casting is relatively low-cost, particularly for small production runs. The materials used (sand and binder) are inexpensive, and the process itself doesn't require extensive investment in specialized equipment.
- Complex Shapes This method enables the casting of complex shapes and large parts that would be challenging or impossible to create using other manufacturing techniques.
- Sustainability Many sand casting factories utilize reclaimed sand in their processes, promoting sustainability and reducing waste.
Conclusion
As a cornerstone of modern manufacturing, sand casting factories play an essential role in producing high-quality metal components across diverse industries. The blend of traditional techniques with innovative practices ensures that sand casting remains relevant in today's fast-paced production environments. Understanding the sand casting process not only emphasizes its importance but also showcases its capabilities in creating intricate and high-quality metal products. With ongoing advancements in technology and processes, sand casting factories are well-positioned to meet the demands of the future.
Post time:ኅዳር . 27, 2024 17:28
Next:Optimizing the Mixture of Resin and Sand for Enhanced Performance in Various Applications