Sand Casting Applications Versatility in Manufacturing
Sand casting, one of the oldest and most versatile metal casting processes, plays a pivotal role in various industries today. This method involves creating a mold out of compacted sand, then pouring molten metal into the mold to create the desired shape. With its unique combination of cost-effectiveness, adaptability, and capability to produce complex shapes, sand casting finds applications across a multitude of sectors.
Historical Context and Basic Process
Dating back thousands of years, sand casting has evolved from rudimentary techniques to sophisticated applications in modern manufacturing. The process begins with creating a mold by compacting sand around a pattern, which is often made from wood, metal, or plastic. The pattern is then removed, leaving a cavity in the sand that reflects the shape of the final product. Molten metal is poured into this cavity, and once cooled and solidified, the mold is broken apart, allowing for the extraction of the finished casting.
Applications in the Automotive Industry
One of the most significant applications of sand casting is in the automotive industry. Automakers use sand casting to produce engine blocks, cylinder heads, and transmission cases. The ability to create intricate designs and complex geometries makes sand casting ideal for manufacturing parts that need to withstand high stress and extreme temperatures. Additionally, the process allows for the economical production of both small and large components, catering to mass production needs as well as custom orders.
For example, companies often rely on sand casting for producing components like exhaust manifolds and water pumps. The versatility in manipulating the sand mixture allows manufacturers to fine-tune the material properties, achieving desired strength and durability based on the specific operational requirements.
Aerospace and Defense Applications
The aerospace and defense sectors also benefit significantly from sand casting. Components such as turbine casings, structural parts, and engine mountings are often produced using this method. The lightweight yet strong properties of certain metal alloys used in sand casting are particularly valued in these applications, where performance and efficiency are critical.
sand casting applications
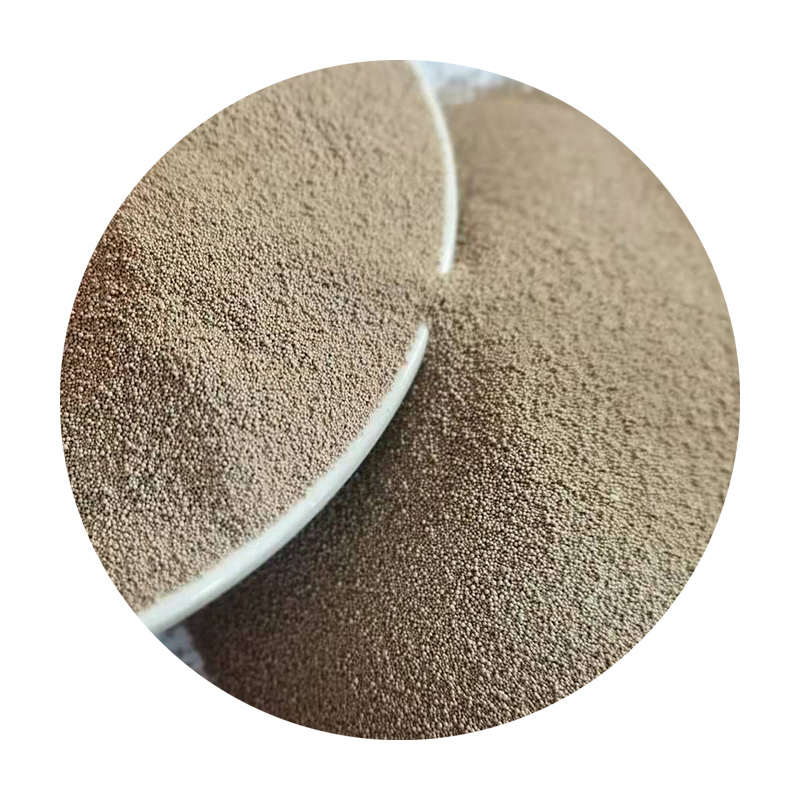
Furthermore, castings produced through sand casting can endure extreme environmental conditions, making them suitable for aircraft and spacecraft components. This fact highlights not only the functional benefits of sand casting but also its role in advancing technology in high-stakes environments.
Industrial Machinery and Equipment
In the realm of industrial machinery, sand casting is essential for producing a variety of components such as gears, valves, and housings. Every sector that relies on machinery benefits from the durability and customizability of cast parts. With the rise of automation and advanced manufacturing technologies, sand casting has adapted, incorporating precision machining to enhance the quality of finished parts.
Also, the ability to produce large components in a single piece makes sand casting ideal for heavy machinery used in construction, mining, and agriculture. The process can support manufacturing large castings for equipment like bulldozers and excavators, providing manufacturers with the needed strength and integrity.
Artistic and Decorative Uses
Beyond industrial applications, sand casting is also employed in artistic endeavors. Sculptors utilize sand casting to create sculptures and decorative items, showcasing the aesthetic potential of metalwork. The process allows artisans to experiment with shapes and textures, producing unique art pieces that merge functionality with beauty.
Furthermore, the popularity of custom-designed elements in modern architecture has seen an increase in sand-cast decorative components, from facade elements to custom railings. Artists appreciate the flexibility that sand casting provides, enabling them to bring their creative visions to reality.
Conclusion
In summary, sand casting stands as a robust and versatile manufacturing process, applicable across various sectors. From automotive and aerospace to industrial machinery and artistic applications, its advantages in producing intricate designs, accommodating diverse materials, and enabling both mass and custom production highlight its significance in modern manufacturing. As technological advances continue to enhance the efficiency and effectiveness of sand casting, its importance in producing high-quality castings will likely grow, ensuring that this ancient technique persists in our cutting-edge industrial landscape.
Post time:ታኅሣ . 13, 2024 14:43
Next:ceramic foundry sand