Sand Cast Foundry A Comprehensive Overview
Sand casting, also known as sand mold casting, is one of the oldest and most versatile manufacturing processes used to create metal components. Industries ranging from automotive to aerospace utilize this technique due to its ability to produce complex shapes with high precision. This article delves into the fundamentals of sand cast foundries, exploring their processes, advantages, and applications.
The Sand Casting Process
At the core of sand casting is the use of a sand mold to shape molten metal. The process begins with the design of a pattern, usually made of wood, metal, or plastic, which mimics the final product. This pattern is crucial as it determines the dimensions and surface finish of the final casted component.
1. Pattern Making The pattern is created with allowances for metal shrinkage and machining needs. It is essential that the pattern accurately reflects the desired end product.
2. Mold Preparation The pattern is then used to form a mold by compacting sand around it. The type of sand used is often a mixture of silica sand, clay, and water, which provides binding properties. The mold typically consists of two halves, known as the cope and drag, which are aligned and clamped together.
3. Melting Metal While the mold is being prepared, the metal, such as aluminum, iron, or bronze, is melted in a furnace. The choice of metal depends on the properties required in the final product.
4. Pouring Once the metal has reached its molten state, it is poured into the mold cavity. Care must be taken to avoid turbulence, which can introduce defects into the cast.
5. Cooling and Solidification After pouring, the metal cools and solidifies to take on the shape of the mold. Cooling times vary based on the size and thickness of the component.
sand cast foundry
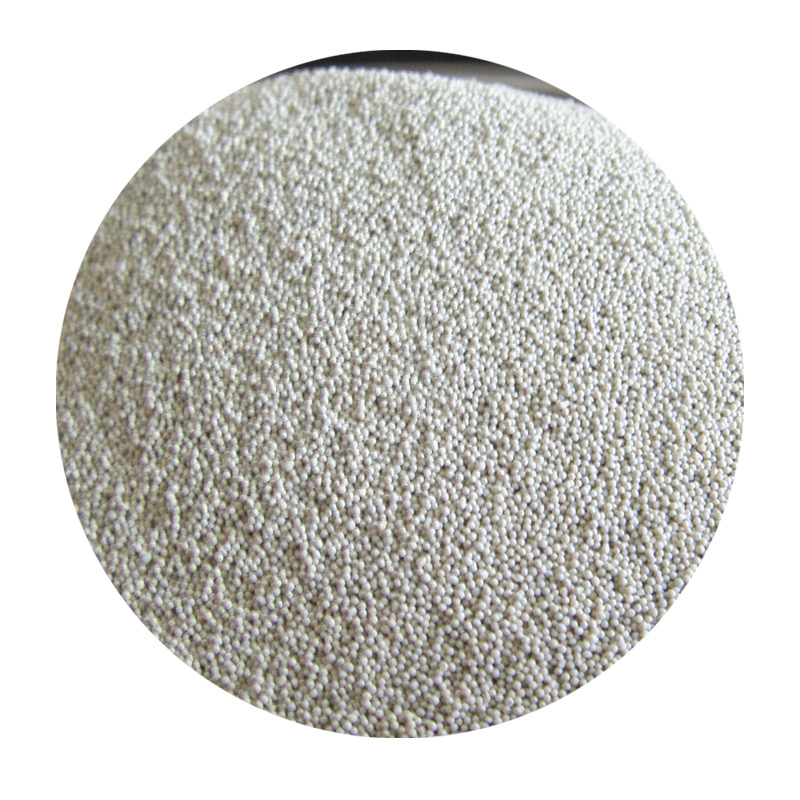
6. Shakeout and Finishing Once the casting has cooled, the sand mold is broken away, revealing the cast part. Depending on the requirements, further finishing processes like grinding, machining, or surface treatment may be necessary to achieve the desired specifications.
Advantages of Sand Casting
Sand casting boasts several advantages that make it a preferred choice in the foundry industry
- Versatility It can accommodate a wide range of metals and is suitable for small to large production runs. - Cost-Effectiveness The materials used (sand and metal) are generally inexpensive, especially when compared to more complex casting methods. - Complex Geometries Sand casting allows for intricate designs and shapes that other manufacturing processes might struggle to replicate. - Reusability The sand used in the mold can often be regenerated and reused, reducing waste and costs.
Applications of Sand Casting
The applications of sand casting are vast and span various industries. In the automotive sector, sand casting is utilized to produce engine blocks, cylinder heads, and other critical components. The aerospace industry also relies on sand casting for parts where lightweight yet robust materials are essential. Additionally, sand cast components are found in agriculture, construction equipment, marine applications, and many more fields.
Conclusion
In conclusion, sand casting remains a fundamental manufacturing process despite the advent of more advanced technologies. Its unique combination of cost-effectiveness, versatility, and capability for producing complex parts ensures its relevance in modern manufacturing. As industries continue to evolve, innovations within the sand casting process, including the use of advanced materials and automation, promise to enhance its efficiency and application reach. Whether you're a manufacturer, engineer, or designer, understanding the dynamics of sand cast foundries is essential in today’s production landscape.
Post time:ኅዳር . 15, 2024 10:39
Next:ang mga hakbang sa paghahagis ng buhangin