The Art and Science of Sand Casting
Sand casting, one of the oldest and most versatile metal casting techniques, has played a crucial role in the development of manufacturing processes. This method, which dates back thousands of years, involves creating a mold from a mixture of sand, clay, and water before pouring molten metal into the cavity to form a desired object. From intricate jewelry to large industrial components, sand casting is a vital process in various industries due to its adaptability and efficiency.
The Basics of Sand Casting
The sand casting process begins with the preparation of a mold. This involves creating a pattern, which is typically made from materials such as wood, metal, or plastic. The pattern replicates the final product and is used to form the cavity in the sand mold. The pattern is then placed in a specially prepared sand mixture, often referred to as green sand, which consists of silica sand, clay, and water. The sand is compacted around the pattern, creating two halves of the mold—known as the cope and the drag.
Once the sand has set and the pattern is removed, the two halves of the mold are reassembled. The mold is then opened at its designated pouring basin, where molten metal will be introduced. Before pouring, allowances for shrinkage and gating systems (paths for the metal to flow) are calculated and incorporated. Choosing the right type of metal is crucial, as different metals have varying melting points, fluidity, and solidification characteristics.
Benefits of Sand Casting
One of the standout features of sand casting is its versatility. This method can accommodate large and small parts with complex geometries, making it suitable for a wide range of applications—from automotive components to artistic sculptures. Additionally, sand molds can be reused multiple times, especially in high-volume production, which enhances both cost-effectiveness and efficiency.
Another significant advantage of sand casting is its relatively low cost. Compared to other casting methods such as investment casting or die casting, the materials required for sand casting are less expensive and more readily available. The simplicity of the sand-casting process means fewer specialized tools and equipment are needed, making it accessible for small businesses and individual artisans alike.
sand caste
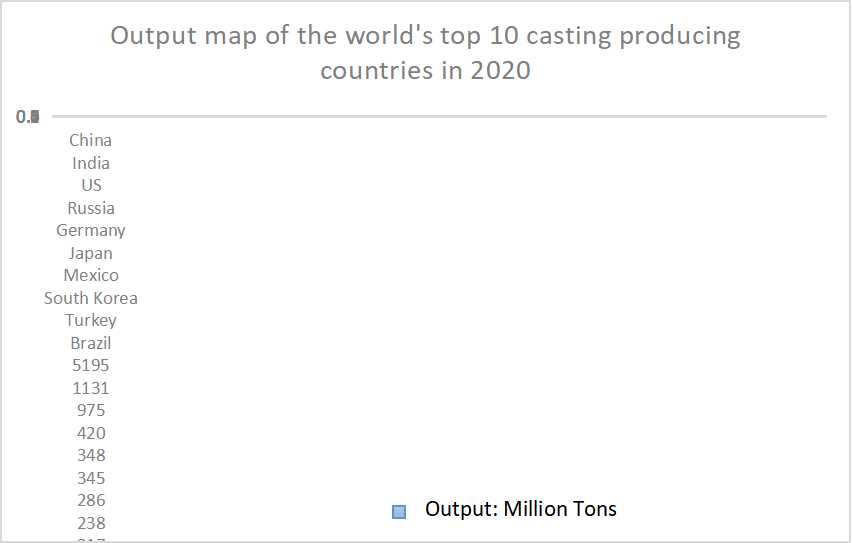
Moreover, sand casting can be easily adapted for various scales of production. Small batches and one-off custom components can be produced with little setup time, while higher volumes can be achieved through improved methodologies and upgraded techniques. This flexibility enables manufacturers to respond swiftly to market demands or specific customer requirements.
Challenges of Sand Casting
Despite its advantages, sand casting does have its share of challenges. One primary concern is the potential for defects in the finished products, such as porosity, sand inclusion, or surface imperfections. These issues can arise from various factors, including improper sand preparation, inadequate pouring technique, or insufficient cooling time. To mitigate these risks, thorough quality control measures must be in place throughout the process.
Another limitation is the surface finish of sand-cast products, which may not be as smooth as those produced through other methods. Additional machining or finishing processes are often required to achieve the desired surface quality, which can add to the overall production time and cost.
The Future of Sand Casting
As industries continue to evolve, so does the sand casting process. Innovations in technology, such as computer-aided design (CAD) and 3D printing, are enhancing the precision and efficiency of sand molds. These advancements allow for more intricate designs and faster production times, bridging the gap between traditional casting techniques and modern manufacturing needs.
Sustainability is also becoming a focal point within the sand casting industry. Efforts to reduce environmental impact are being recognized, including the use of eco-friendly sand mixtures and recycling of materials. These trends reflect a broader movement toward sustainable practices in manufacturing, helping to ensure that sand casting remains relevant in the future.
In conclusion, sand casting is a time-honored technique that continues to evolve to meet modern industry demands. Its strengths in versatility, cost-effectiveness, and ease of use make it an invaluable method for producing goods ranging from everyday items to complex machinery parts. As technology and environmental considerations advance, sand casting is poised to maintain its significance in the world of manufacturing for years to come.
Post time:ኅዳር . 19, 2024 00:54
Next:Techniques for Achieving a Smooth Finish with Clear Resin Sanding