Sand Casting Manufacturing Process A Comprehensive Overview
Sand casting, one of the oldest and most widely used metal casting processes, is a foundational method in manufacturing industries aimed at producing intricate metal parts
. This method employs sand as the primary mold material, making it a versatile and cost-effective solution for creating complex shapes and sizes.The sand casting process begins with the preparation of the sand mixture, which typically consists of silica sand, clay, water, and other additives. The clay acts as a binding agent, providing the necessary cohesiveness to hold the mold together during casting. The mixture is compacted around a pattern—an exact replica of the desired final product—to form the mold. Patterns can be made from various materials, including wood, metal, or plastic, and they are often designed to be slightly larger than the final product to account for material shrinkage.
Once the pattern is prepared and the sand is shaped around it, the next step is to remove the pattern, leaving a cavity in the sand. This cavity will define the shape of the metal part to be cast. Sand molds can be made in two halves, allowing for easier removal and a better finish on the part. After the mold is completed, it is assembled and reinforced to ensure it can withstand the pouring of molten metal.
sand casting manufacturing process
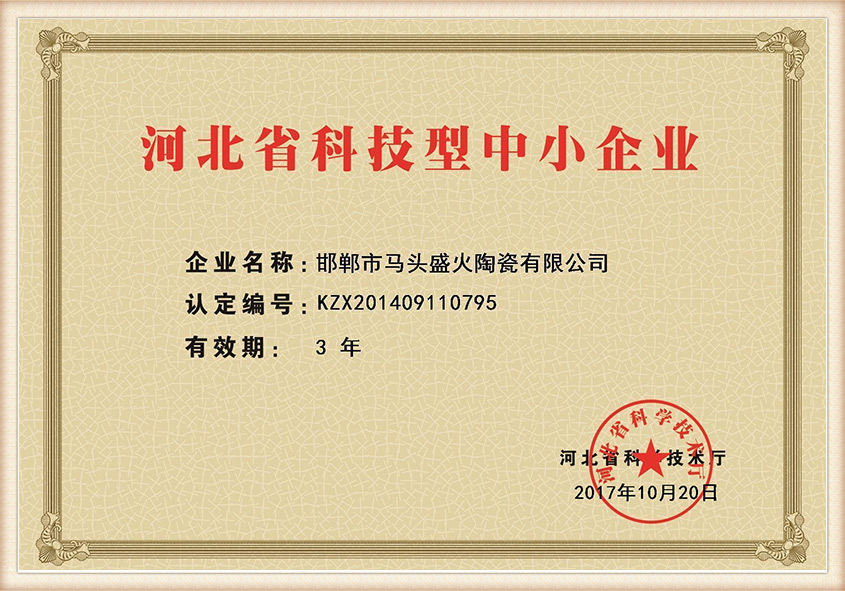
The next phase involves melting the metal, which can be aluminum, iron, bronze, or other alloys, depending on the requirements of the final product. The molten metal is poured into the sand mold through a gating system, which is designed to direct the flow of metal and minimize turbulence. The metal flows into the cavity, filling it completely before being allowed to cool and solidify.
Once the metal has cooled, the mold is broken apart to retrieve the cast part. This is a crucial step in the process, as it requires careful handling to prevent damage to the newly formed part. After extraction, the cast piece often requires additional finishing processes, such as grinding, machining, or surface treatment, to achieve the desired specifications and finish.
One of the advantages of sand casting is its ability to produce large and heavy parts with complex geometries. Additionally, it is suitable for low to medium production runs, making it ideal for prototype development and custom projects. However, there are challenges associated with sand casting, including limitations in dimensional accuracy and surface finish compared to other casting processes, such as investment casting.
In conclusion, sand casting remains a vital manufacturing process with numerous applications across different industries, including automotive, aerospace, and construction. Its adaptability and cost-effectiveness continue to make it a preferred choice for producing diverse metal components, showcasing the ingenuity of traditional manufacturing techniques in modern production.
Post time:መስከ . 01, 2024 11:44
Next:sand casting procedure