The Art and Science of Sand Casting
Sand casting is one of the oldest and most versatile metal casting processes, used to create a wide range of industrial components, artistic sculptures, and intricate designs. This technique dates back thousands of years, with origins traced to ancient civilizations, where sand was utilized to craft molds for metalworking.
At its core, sand casting involves creating a mold from a sand mixture, which is then used to pour molten metal
. The primary materials for the mold are silica sand, clay, and water. The sand is mixed with a binding agent, allowing it to hold its shape when compacted around a pattern—typically a replica of the object to be cast. The process begins by forming a mold in two halves, which can be easily separated once the metal solidifies.One of the key advantages of sand casting is its ability to accommodate complex geometries and large sizes. Unlike other casting methods, sand casting can produce items ranging from small components to massive parts used in heavy machinery. The flexibility of sand molds allows for the incorporation of intricate details, making it a preferred choice in industries such as automotive, aerospace, and art.
sand cast
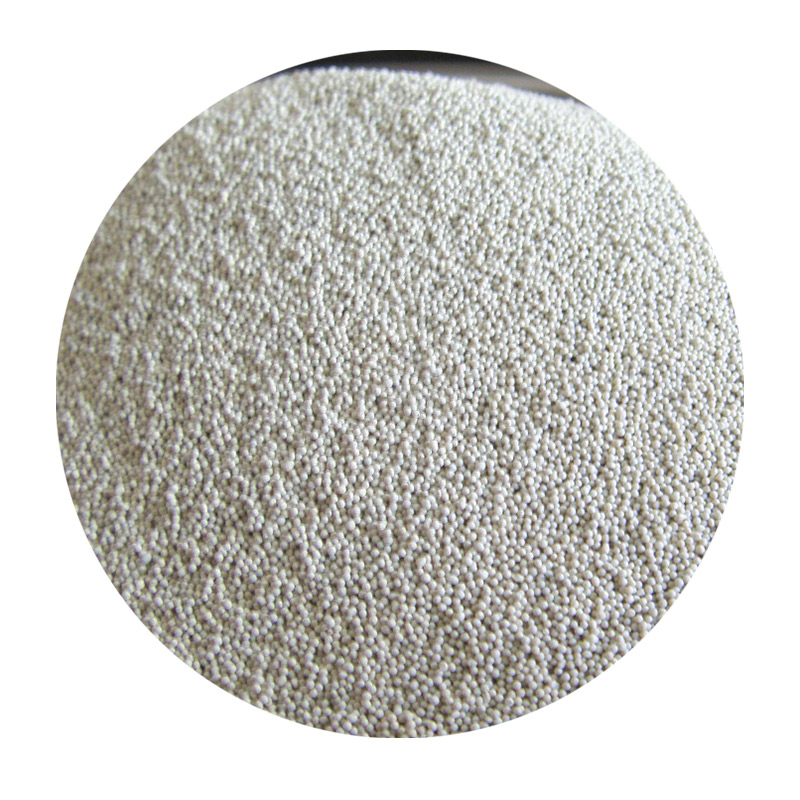
The pouring of molten metal into the mold is a critical phase of the process. Careful temperature control and pouring techniques must be maintained to prevent defects such as air pockets or metal solidification too soon. Once the metal is poured, it is allowed to cool and solidify. Following this, the mold material is removed, revealing the final cast. This step often involves various techniques, including shaking out the sand and using mechanical systems for larger objects.
After removing the casting from the mold, post-processing operations such as grinding, machining, and surface finishing may be required to achieve the desired finish and dimensional accuracy. Sand casting is also environmentally friendly; the sand can often be reused multiple times with minimal waste.
While advancements in technology have introduced newer methods of metal casting, sand casting remains a popular choice due to its cost-effectiveness and adaptability to different metals and alloys. From functional parts to artistic creations, sand casting continues to play a vital role in our modern manufacturing landscape. Its blend of simplicity and effectiveness ensures that it will remain relevant for years to come.
Post time:መስከ . 06, 2024 02:42
Next:Sand Used in Sand Casting