Low Pressure Sand Casting A Comprehensive Overview
Low pressure sand casting is a specialized foundry process that has gained significant popularity in recent years for its efficiency and ability to produce high-quality components. This technique is used primarily for manufacturing complex parts made from metal alloys, particularly aluminum, which are essential in various industries including automotive, aerospace, and machinery. The low-pressure method combines the traditional sand casting processes with the advantages of controlled pressure application, resulting in improved material properties and reduced defects.
Understanding the Process
The low pressure sand casting process involves several steps that contribute to its effectiveness. Firstly, a mold is created using sand mixed with a binding agent. The sand mold is formed around a pattern that represents the final part. Unlike traditional sand casting, which relies on gravity to fill the mold, low pressure casting utilizes a pressurized system to introduce molten metal into the mold cavity. This is achieved by placing the sand mold in an enclosed chamber, where the molten metal is introduced at low pressure, typically ranging from 0.1 to 0.3 bar.
This method of using low pressure allows for a more controlled filling of the mold and minimizes the risk of turbulence that can lead to defects such as air entrapment and inclusions. As the molten metal fills the mold from the bottom up, it displaces air in a controlled manner, ensuring that the cast component is dense and free from voids.
Advantages of Low Pressure Sand Casting
1. Improved Quality One of the primary advantages of low pressure sand casting is the quality of the finished product. The controlled pressure flow results in a smoother surface finish and enhanced dimensional accuracy. The process also minimizes defects associated with traditional sand casting methods, such as shrinkage and porosity.
2. Complex Geometries Low pressure sand casting is particularly effective for producing components with intricate designs. The pressurized approach allows for better filling of complex features, enabling manufacturers to create parts that would be difficult or impossible to achieve through conventional casting methods.
low pressure sand casting
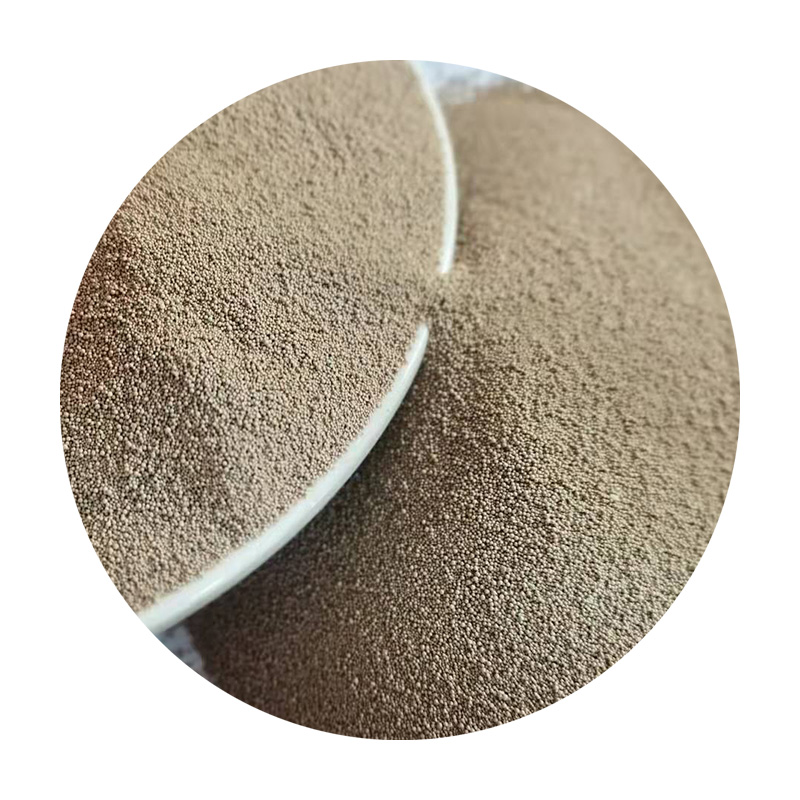
3. Material Efficiency This method results in less waste material compared to traditional techniques. The precise control over the filling process means that the amount of molten metal used can be optimized, reducing excess material and thus lowering costs.
4. Versatility The process can accommodate various types of alloys, making it an ideal choice for producing both ferrous and non-ferrous metals. This versatility allows manufacturers to select the best material for their specific application.
5. Shorter Lead Times Low pressure sand casting can lead to quicker production cycles due to the faster cooling rates observed with aluminum alloys. This is beneficial for businesses seeking to reduce lead times and meet customer demands swiftly.
Applications in Industry
Given its numerous advantages, low pressure sand casting has found applications in various sectors. The automotive industry utilizes this process for producing engine components, wheels, and other critical parts. In aerospace, low pressure casting is used for manufacturing lightweight yet strong structural components that can withstand harsh conditions. It is also used in the production of machinery parts where precise tolerances and strength are required.
Conclusion
Low pressure sand casting is an innovative and efficient method that has revolutionized the foundry industry. By combining traditional sand casting techniques with modern pressure control technology, manufacturers can produce high-quality, complex components with less waste and fewer defects. As industries continue to evolve and demand higher standards for product performance, low pressure sand casting will likely play an increasingly significant role in meeting these challenges. Its ability to offer superior material characteristics while maintaining cost-effectiveness makes it a vital process for future manufacturing endeavors.
Post time:ጥቅም . 17, 2024 09:33
Next:what type of sand is used for sand casting