Lost Foam Casting Coating An Overview
Lost foam casting (LFC) is an innovative method that integrates the simplicity of traditional casting with modern technology to produce highly accurate and complex metal parts. One of the critical components in this process is the coating used to cover the foam pattern before it is subjected to molten metal. This article explores the significance of the coating in lost foam casting, its composition, and its impact on the final output.
Lost Foam Casting Coating An Overview
Typically, the coating consists of a mixture of fine sand and a binding agent, usually a type of phenolic resin. The sand provides thermal resistance, while the resin binds the particles together to form a strong shell. The thickness of this coating is crucial; it must be substantial enough to withstand the heat and pressure of the molten metal while remaining thin enough not to hinder the precision of the final casting. Advanced formulations may include additives that enhance the coating's properties, such as increasing its strength, thermal stability, or even its ease of application.
lost foam casting coating
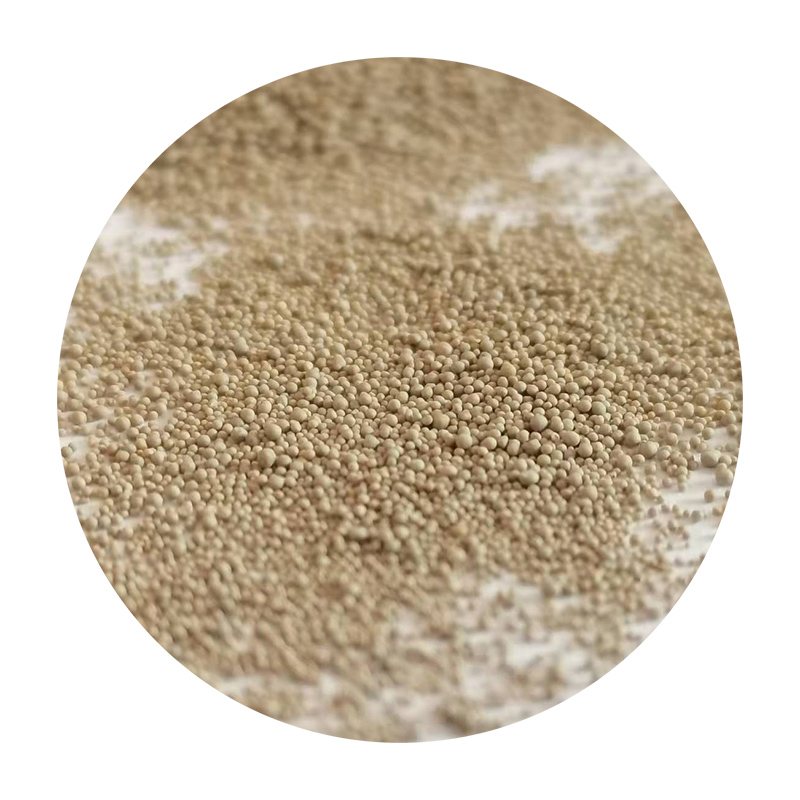
Another essential aspect of the coating process is its impact on the final surface finish of the cast part. The smoother the coating, the better the surface quality of the finished metal product. Poorly applied or rough coatings can result in defects on the cast surface, leading to additional machining or finishing work, which increases production costs. Therefore, achieving a balance between coating strength and surface smoothness is crucial for successful lost foam casting.
Moreover, the coating's composition influences the casting process's overall efficiency. The right combination of materials can optimize the curing time, making it faster to apply and allowing for higher production rates. This efficiency is particularly beneficial in industries where time equals money, such as automotive or aerospace manufacturing.
In conclusion, the coating in lost foam casting plays an indispensable role in ensuring a successful cast. It not only protects the foam pattern from extreme temperatures but also contributes to the surface quality and overall efficiency of the process. As industries continue to push for more complex geometries and tighter tolerances, innovations in coating materials and techniques will be pivotal. The future of lost foam casting will likely see advancements that enhance its versatility and effectiveness, making it a go-to method for precision metal parts manufacturing.
Post time:ጥቅም . 17, 2024 02:58
Next:Techniques for Wet Sanding Ceramics to Achieve a Smooth Finish