Lost foam metal casting is an innovative and efficient casting process that has gained considerable traction in the manufacturing industry. This method stands out due to its unique approach to creating complex metal parts with high precision and minimal waste. In essence, lost foam casting merges the advantages of traditional sand casting with modern technology to produce high-quality components for various applications.
The process begins with a foam pattern made from polystyrene or similar materials, which is designed to replicate the shape and features of the final metal product. Unlike conventional casting methods that use metal molds, lost foam casting employs these foam patterns directly in the casting process. The foam pattern is coated with a thin layer of sand, which is then compacted to form a mold around it. Once the mold is created, molten metal is poured into the cavity created by the foam pattern.
As the molten metal fills the mold, the heat causes the foam to evaporate, hence the term lost foam. This process offers several advantages, the most notable being the ability to achieve intricate geometries and excellent surface finishes. Moreover, because the foam material disappears without leaving any residue, there is no need for elaborate core or intricate gating systems. This simplification reduces manufacturing costs and time while increasing the overall efficiency of production.
lost foam metal casting
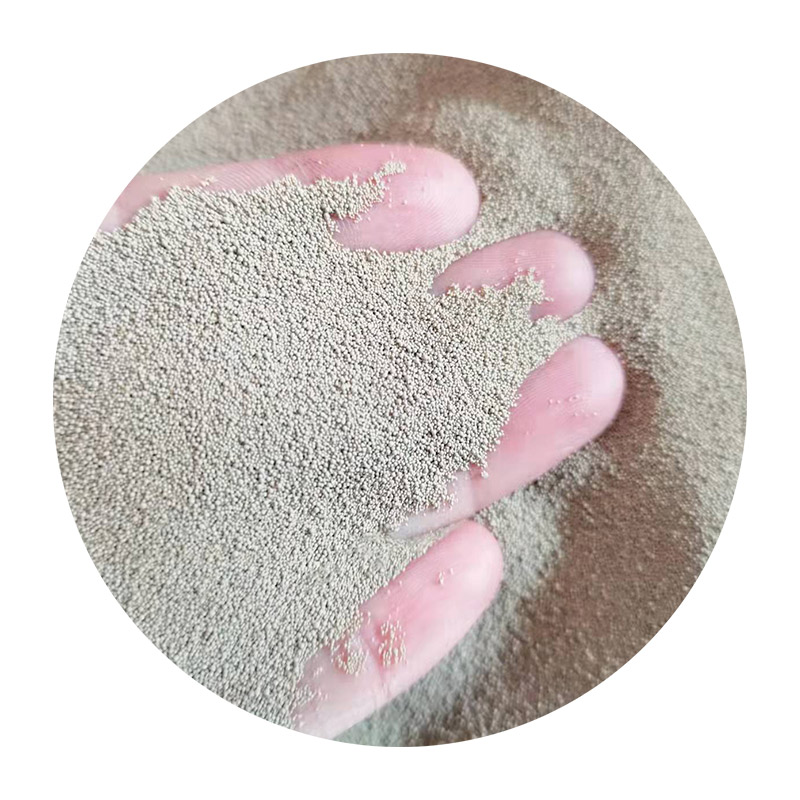
One of the key benefits of lost foam casting is its capability to produce parts with complex features, which would be challenging or impossible to achieve using traditional casting methods. This makes it an ideal choice for industries such as automotive, aerospace, and aerospace where intricate designs and lightweight components are essential. The process also reduces the amount of machining required after casting, further optimizing production efficiency.
Additionally, lost foam metal casting is an environmentally friendly option. The use of foam patterns eliminates the need for molds made from sand and metal, which often require significant energy to create and dispose of. Since the foam is converted to gas during the casting process, there is less waste, making it a sustainable choice for manufacturers aiming to reduce their environmental footprint.
In conclusion, lost foam metal casting represents a significant advancement in manufacturing technology. Its ability to produce complex, high-precision parts with reduced waste makes it an attractive alternative to traditional casting methods. As industries continue to seek innovative solutions to enhance efficiency and reduce costs, lost foam casting is likely to become an increasingly popular choice in the world of metal casting. Its unique advantages pave the way for a future where intricate designs meet sustainable practices, ensuring that the manufacturing landscape is both advanced and environmentally conscious.
Post time:መስከ . 12, 2024 15:23
Next:Excellence in Metal Casting with Ceramsite Foundry Sand