Investment Casting vs. Sand Casting A Comparative Analysis
When it comes to metal casting processes, investment casting and sand casting are two prevalent methods, each with its unique advantages and disadvantages. Understanding the differences between these two techniques is essential for manufacturers and engineers who aim to optimize their production processes for specific applications. This article explores investment casting and sand casting, focusing on their respective characteristics, costs, and applications.
Investment Casting Precision and Complexity
Investment casting, also known as lost-wax casting, is a highly precise method that allows for the creation of intricate designs with tight tolerances. This process begins with creating a wax model of the desired part, which is then coated in a ceramic material to form a mold. Once the mold is set, the wax is melted away, leaving a cavity into which molten metal is poured. The precision of investment casting makes it ideal for producing complex geometries, intricate details, and thin-walled components.
One of the significant advantages of investment casting is the high-quality surface finish it provides. Parts produced through this method often require minimal machining, reducing overall manufacturing time and costs. However, this precision does come at a price; investment casting tends to be more expensive than sand casting, particularly for low-volume production runs. The complexity of the mold-making process, along with the need for specialized equipment, contributes to the higher costs.
Investment casting is commonly used in the aerospace, medical, and automotive industries, where precision and reliability are paramount. Components such as turbine blades, surgical instruments, and precision gears are often manufactured using this method due to their demanding specifications.
Sand Casting Versatility and Cost-Effectiveness
investment vs sand casting
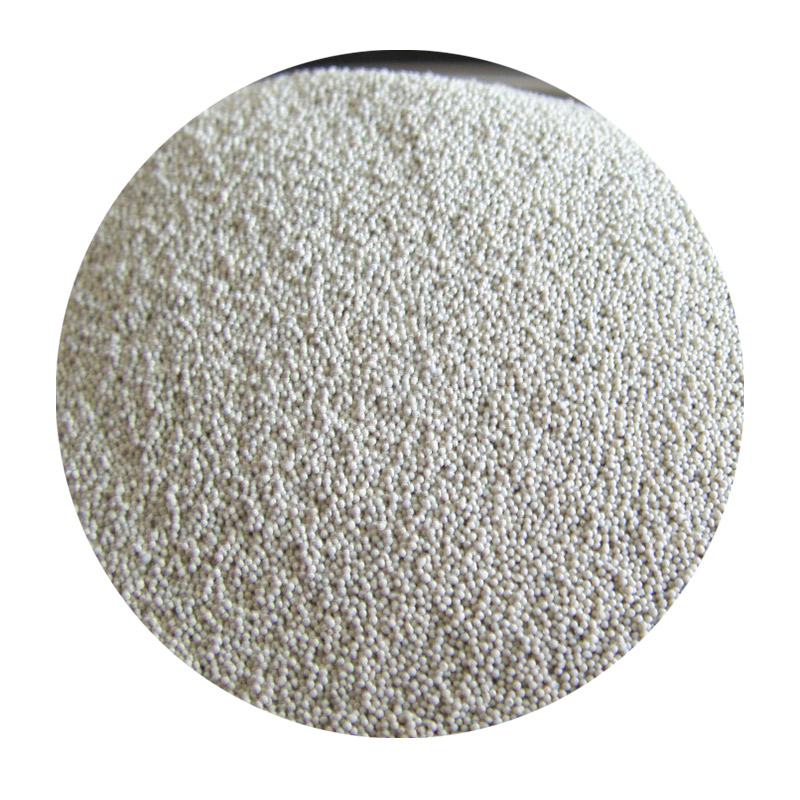
On the other hand, sand casting is a versatile and cost-effective method that is suitable for producing larger parts or those that do not require the same level of detail as investment casting. This process involves creating a mold from a mixture of sand and a binding agent. A pattern of the desired object is pressed into the sand to create a cavity. Once the mold is prepared, molten metal is poured into the cavity, allowed to cool, and then removed.
One of the primary advantages of sand casting is its lower cost, especially for large-volume production runs. The materials needed for sand casting are relatively inexpensive, and the molds can be produced more quickly than those required for investment casting. Furthermore, because sand molds are reusable, manufacturers can produce various parts without significant additional expenses.
However, sand casting does have its limitations. The surface finish and dimensional accuracy are generally not as high as those achieved through investment casting. Parts produced via sand casting often require additional machining to meet the required specifications, which can add to the overall production time.
Sand casting is widely used across various industries, including construction, agriculture, and the production of automotive components. It is particularly effective for creating large, heavy parts like engine blocks, frames, and housings.
Conclusion Choosing the Right Method
In conclusion, the choice between investment casting and sand casting largely depends on the specific requirements of the project at hand. If precision, intricate design, and superior surface finish are priorities, investment casting may be the preferred option, despite its higher cost. Conversely, if cost-effectiveness and the ability to produce larger or simpler parts are more important, sand casting is likely the better choice. Ultimately, understanding the strengths and limitations of each method will aid manufacturers in making informed decisions to optimize their production processes and meet their design goals effectively.
Post time:ታኅሣ . 19, 2024 18:30
Next:furan resin sand casting