When it comes to metal casting processes, two popular methods are die casting and sand casting. Both techniques have their unique advantages and applications, but they differ significantly in terms of material, process, cost, and final product characteristics.
Die casting involves forcing molten metal into a mold under high pressure, allowing for the creation of intricate shapes with smooth surfaces. This method is typically used for non-ferrous metals, such as aluminum, zinc, and magnesium. The molds in die casting are made of steel or other durable materials, which can withstand the high-pressure injection process. As a result, die casting is ideal for high-volume production, as it can produce thousands of uniform parts in a relatively short period. Additionally, the surface finish in die casting is often superior, requiring little to no machining after production.
In contrast, sand casting is a more traditional method where a sand-based mold is created to form the final shape. This process can accommodate a wide range of metals, including iron and steel, along with non-ferrous alloys. Sand casting is versatile and can produce large parts with complex geometries. However, the surface finish is typically rougher than die casting, often necessitating additional machining to achieve the desired finish. One of the key advantages of sand casting is its lower cost for less complex shapes and smaller production runs; the molds are made from sand, which is inexpensive and easy to form.
difference between die casting and sand casting
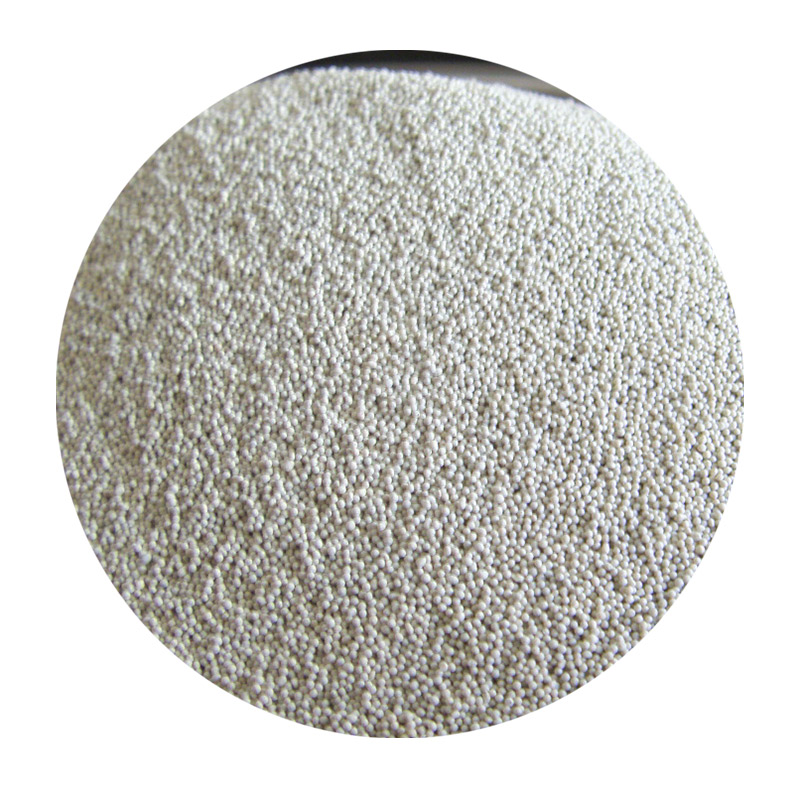
The differences in cost and production volume are significant between the two methods. Die casting requires a higher initial investment for mold creation, making it less economical for small batches. However, for mass production, die casting becomes cost-effective due to its speed and efficiency. On the other hand, sand casting offers a more economical solution for small to medium production runs and is particularly advantageous for larger parts that would be uneconomical to produce via die casting.
Furthermore, the mechanical properties of the final products can differ. Die cast components generally have better dimensional accuracy and tighter tolerances, which can be crucial for certain applications. Sand casting, while offering more flexibility in terms of material choice, may produce parts with variability in strength and finish.
In summary, the choice between die casting and sand casting largely depends on the specific requirements of the project, including production volume, material type, budget constraints, and desired final product quality. Understanding these differences enables manufacturers to select the most suitable casting method for their needs.
Post time:መስከ . 11, 2024 01:42
Next:Heath Ceramics Sand Collection | Timeless Elegance in Ceramics