Understanding the Density of Foundry Sand
Foundry sand plays a crucial role in the casting process, serving as a mold material that shapes molten metal into various forms. As industries ranging from automotive to aerospace continue to demand precision cast parts, understanding the properties of foundry sand, particularly its density, becomes essential for optimizing casting performance and ensuring quality outcomes.
What is Foundry Sand?
Foundry sand is specifically formulated sand utilized for creating molds and cores in metal casting. The most commonly used type is silica sand, due to its high melting point, low expansion rate, and availability. Foundry sands can be natural or synthetic, with natural sand being derived from water-washed deposits and synthetic sand being processed and treated to meet specific requirements.
The Importance of Density
Density, defined as mass per unit volume, is a fundamental property of materials that influences various factors in foundry operations. For foundry sand, the density plays a significant role in determining the sand's ability to retain shape under high temperatures, its flowability, and its ease of handling.
1. Casting Quality The density of foundry sand directly affects the molding process and the final quality of castings. Higher density sands can provide better dimensional accuracy as they resist deformation during the pouring of molten metal. This characteristic minimizes casting defects, such as misalignment or warping.
2. Thermal Properties Density also correlates with thermal performance. Sands with appropriate density and grain size facilitate better heat distribution during casting. This results in improved cooling rates and helps to achieve finer grain structures in the finished casting, enhancing surface finish and mechanical properties.
3. Mold Strength Proper density ensures that the mold possesses adequate strength to withstand the pressure of the molten metal. Low-density sands might crumble or break under stress, leading to defects such as inclusions or even core collapses during casting.
Measuring Density
Density of foundry sand can be measured using several methods
density of foundry sand
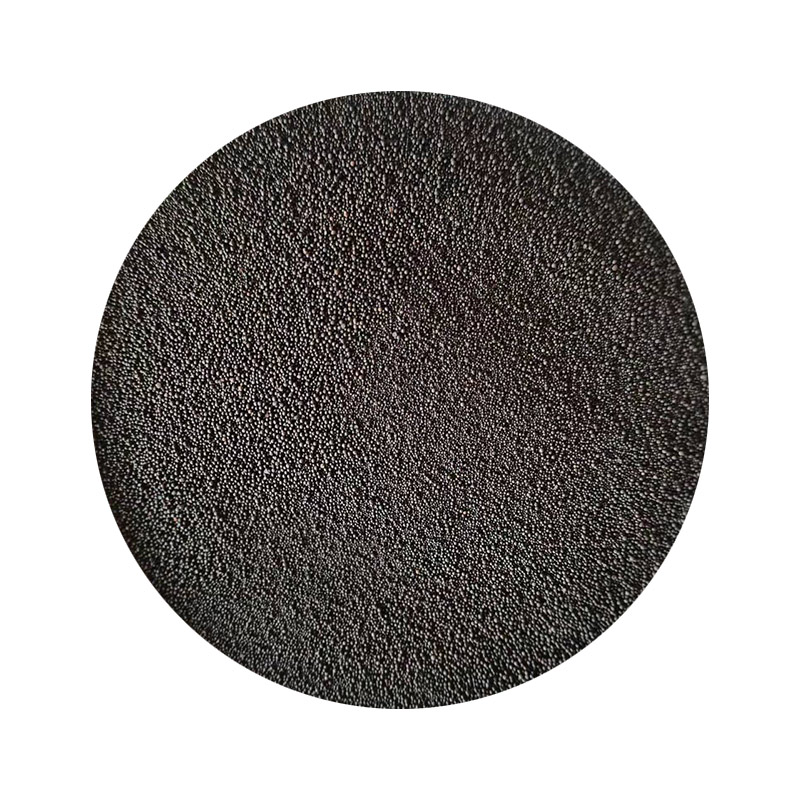
- Bulk Density This is determined by measuring the mass of a known volume of sand, typically in a graduated cylinder. The bulk density reflects how the sand will behave in a mold and is crucial for calculating material requirements.
- Tapped Density The tapped density is measured after mechanically tapping the sand to mimic settling effects. It provides insight into how the sand’s packing efficiency changes, thereby contributing to mold stability.
- Loose Density Involves measuring the sand in its natural, unpacked state
. This measurement helps in understanding how the sand behaves when poured or stacked.Each of these densities provides valuable information and can be influenced by the sand's grain size, shape, and moisture content.
Key Factors Influencing Density
The density of foundry sand is affected by several factors
1. Grain Size and Shape Finer sands tend to have higher densities due to reduced void space between grains. Meanwhile, irregularly shaped grains can lead to lower densities because of poor packing efficiency.
2. Moisture Content The presence of water in sand can affect its density by increasing the overall weight per unit volume. However, excessive moisture can lead to poor mold strength and potential casting defects.
3. Additives The incorporation of bonding agents or clay can alter the density of the sand mix, enhancing its properties for specific applications.
Conclusion
Understanding the density of foundry sand is paramount for achieving optimal results in metal casting. It influences mold quality, casting accuracy, and the overall performance of the foundry process. By carefully measuring and adjusting the density through various techniques and methods, foundries can ensure high-quality output, reduce defects, and meet the demanding specifications of modern casting applications. As technology continues to advance, ongoing research into the properties and applications of foundry sand will further enhance the efficiency and effectiveness of metal casting processes worldwide.
Post time:ኅዳር . 27, 2024 21:27
Next:An Overview of Sand Casting Techniques in Engineering Applications