3D Printing in Sand Casting Revolutionizing Traditional Manufacturing
In recent years, the manufacturing industry has witnessed a significant transformation driven by advancements in technology. Among the most innovative developments is the integration of 3D printing into traditional sand casting processes. This hybrid approach combines the benefits of additive manufacturing with the established techniques of foundry work, resulting in enhanced efficiency, cost-effectiveness, and design versatility.
Sand casting has long been a popular choice in metalworking due to its ability to create complex shapes at a relatively low cost. The process involves creating a mold from sand, into which molten metal is poured. However, traditional sand casting can be time-consuming and requires significant setup, particularly for intricate designs. This is where 3D printing comes into play, offering a solution that streamlines the mold-making process and overcomes many limitations of conventional methods.
3D Printing in Sand Casting Revolutionizing Traditional Manufacturing
Another significant benefit is the design freedom that 3D printing provides. Traditional sand casting is often restricted by the limitations of the mold design, which may necessitate draft angles or other features to facilitate mold removal. With 3D printing, these constraints are greatly alleviated. Designers can create complex geometries that would be impossible or prohibitively expensive with traditional methods. This opens up new possibilities for product innovation, allowing engineers to explore designs that optimize performance while reducing material usage.
3d printing sand casting
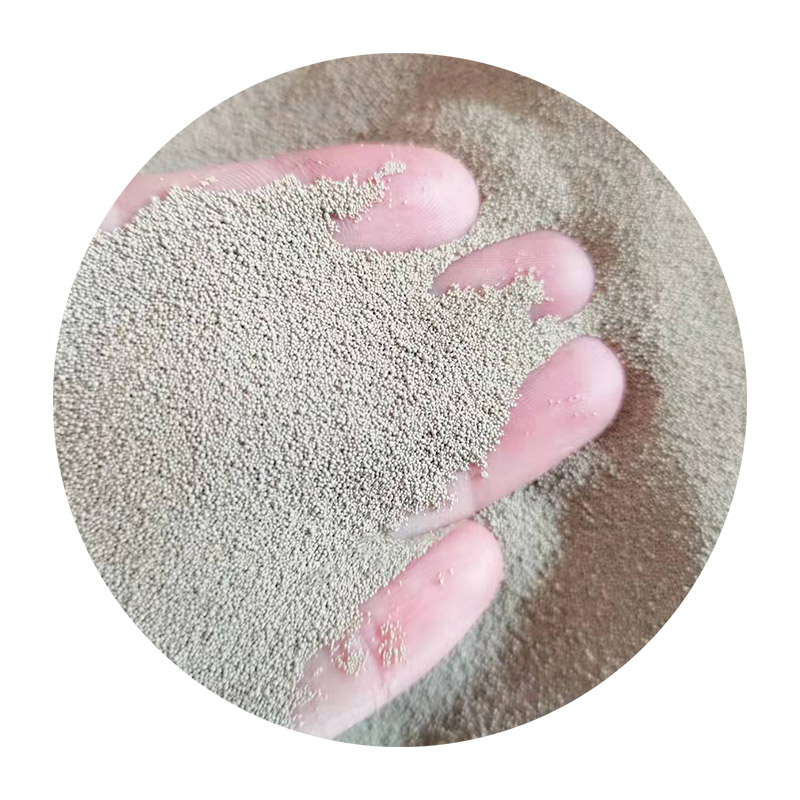
Additionally, 3D printing enables the production of molds with integrated cooling channels and other features that enhance the casting process. These advanced designs can lead to improved cooling rates and reduced defects in the final product, such as warping or porosity. This is particularly beneficial for industries where precision is critical, such as aerospace, automotive, and medical applications.
Cost savings also play a crucial role in the adoption of 3D printing for sand casting. By reducing material waste and minimizing the need for extensive labor, companies can lower their overall production costs. Furthermore, the ability to produce smaller batches of customized parts without the need for extensive tooling means that businesses can cater to niche markets more effectively, thus diversifying their revenue streams.
While the integration of 3D printing into sand casting is not without challenges, such as the need for specialized equipment and materials, the benefits it offers are compelling. As the technology continues to evolve, we can expect to see further advancements in materials and methods that will make this hybrid approach even more viable.
In conclusion, the intersection of 3D printing and sand casting is reshaping the landscape of manufacturing. By leveraging the strengths of both technologies, manufacturers can achieve greater efficiency, reduce lead times, and unleash new creative possibilities in design. As industries continue to embrace these innovations, the future of sand casting is likely to be as dynamic and adaptable as the technologies that support it. This evolution not only enhances production capabilities but also paves the way for more sustainable manufacturing practices, marking a significant step forward in the industry.
Post time:መስከ . 29, 2024 00:28
Next:Exploring Low Pressure Sand Casting Techniques for Enhanced Manufacturing Efficiency and Quality