The Synergy of 3D Printing and Sand Casting Revolutionizing Manufacturing Processes
In recent years, the manufacturing landscape has undergone a significant transformation, driven largely by advancements in technology. One of the most promising developments has been the integration of 3D printing with traditional sand casting techniques. This hybrid approach not only enhances the efficiency of production processes but also enables manufacturers to create complex geometries that were previously considered impractical.
3D printing, also known as additive manufacturing, involves building objects layer by layer from a digital model. This technique is lauded for its flexibility, allowing designers to easily modify their creations without the need for expensive tooling changes. Sand casting, on the other hand, has been a staple in manufacturing for centuries, where molten metal is poured into a sand mold to form various components. While effective, the traditional sand casting process is often hampered by limitations such as extended lead times, high tooling costs, and the challenges of achieving intricate designs.
The Synergy of 3D Printing and Sand Casting Revolutionizing Manufacturing Processes
Moreover, 3D printed sand molds can achieve complex internal geometries that are challenging to produce using traditional methods. This capability opens new avenues for design innovation, enabling the creation of lightweight yet robust components. As industries such as aerospace and automotive increasingly prioritize weight reduction for fuel efficiency, the ability to produce geometrically optimized parts becomes indispensable.
3d printing sand casting
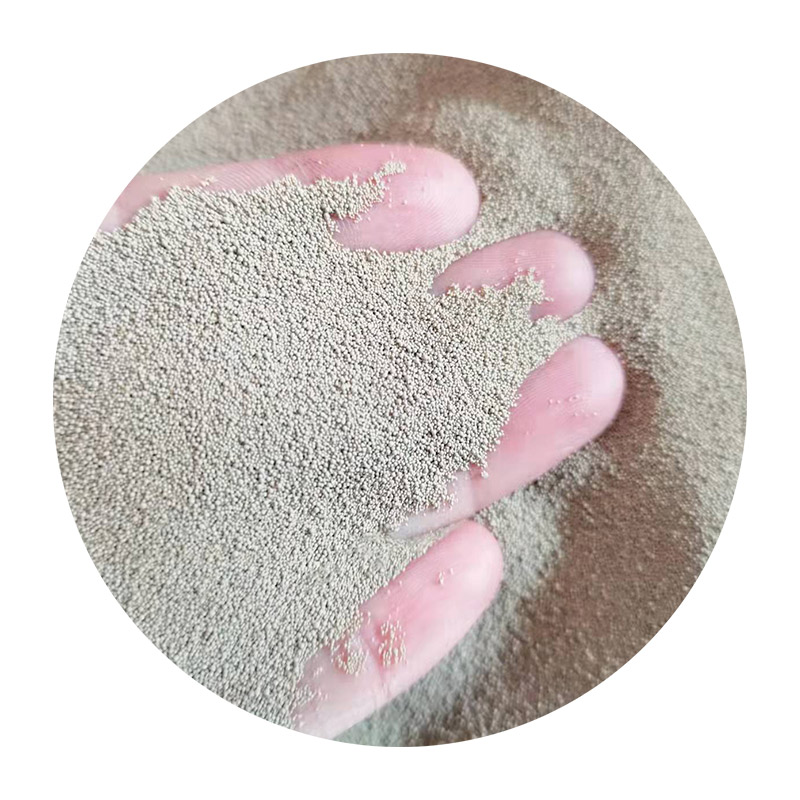
The environmental impact of manufacturing processes is another critical consideration today. Traditional sand casting generates a significant amount of waste. However, when combined with 3D printing, this process can minimize material waste substantially. The precise nature of 3D printing means that only the necessary amount of material is used to create each mold, and many 3D printing techniques allow for the recycling of sand, further reducing the environmental footprint.
Additionally, the use of 3D printed sand molds enhances the repeatability and consistency of the casting process. Traditional methods often lead to variations in product quality due to inconsistencies in mold production. However, with 3D printing, the digital file can guarantee that each mold is produced with the same specifications, resulting in higher quality and more reliable end products.
Several industries are beginning to embrace this innovative approach. For example, leading manufacturers in the automotive sector are utilizing 3D printing for sand casting to produce engine components that are not only lighter but also more efficient. Similarly, the aerospace industry is leveraging this technology to create parts that meet strict safety and performance standards while minimizing waste.
In conclusion, the synergy of 3D printing and sand casting has the potential to revolutionize the manufacturing industry. By combining the design flexibility and rapid prototyping capabilities of 3D printing with the time-tested reliability of sand casting, manufacturers can improve efficiency, reduce costs, and foster innovation. As this technology continues to evolve, we can expect to see even more groundbreaking developments that will reshape our understanding of what is possible in manufacturing. The future is promising, and industries that adopt this hybrid approach will likely lead the way in creating the next generation of products.
Post time:ጥቅም . 10, 2024 16:26
Next:sanding 3d print