3D Sand Printing Casting Revolutionizing the Foundry Industry
The advent of 3D printing technology has sparked a paradigm shift across various industries, and the foundry sector is no exception. Among the innovative techniques emerging in this space is 3D sand printing casting, a process that combines the benefits of additive manufacturing with traditional casting methods. This technology promises to enhance efficiency, reduce costs, and offer greater design flexibility, marking a significant improvement over conventional foundry practices.
3D Sand Printing Casting Revolutionizing the Foundry Industry
One of the most compelling advantages of 3D sand printing is its ability to produce molds with intricate internal features. This capability allows for the creation of lightweight structures that maintain strength while optimizing material usage. Such designs can lead to significant weight reductions in automotive and aerospace components, ultimately contributing to improved fuel efficiency and performance.
3d sand printing casting
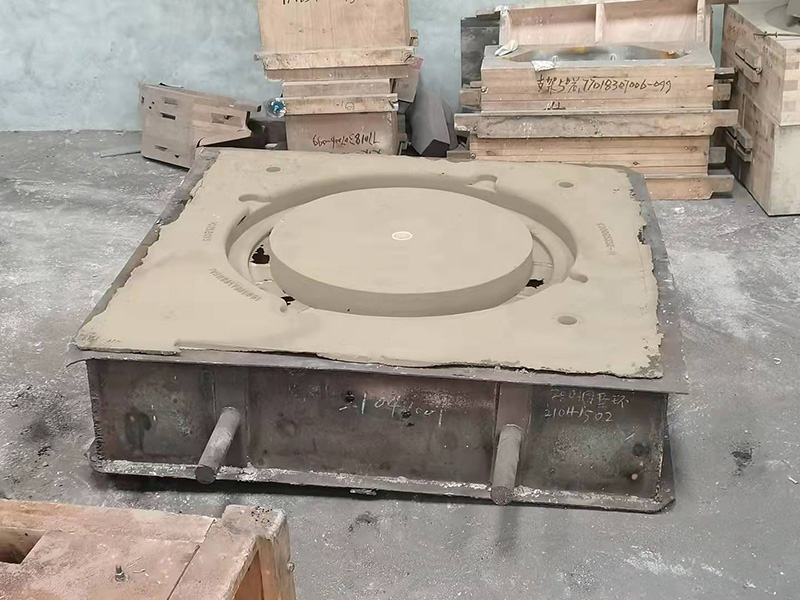
Additionally, the reduction in lead times is a game-changer for the foundry industry. Traditional mold-making processes can take weeks or even months, as they often require the fabrication of physical patterns. In contrast, 3D sand printing can produce molds within hours, significantly accelerating the production timeline. This speed not only enhances responsiveness to market demands but also allows for rapid prototyping and iterative design processes, enabling engineers to test and refine their designs more efficiently.
Cost-effectiveness is another critical benefit that 3D sand printing offers. By eliminating the need for complex tooling and reducing material waste, manufacturers can lower their overall production costs. Furthermore, the ability to create molds on-demand reduces the need for large inventories of pre-made molds, which can become obsolete as design specifications change. This on-demand production model aligns well with the growing trend towards customization in various industries, paving the way for personalized and unique products.
Moreover, 3D sand printing technology is environmentally friendly. Traditional casting methods often result in a significant amount of waste, while the additive nature of 3D printing ensures that materials are used efficiently. As manufacturers strive to adopt sustainable practices, 3D sand printing stands out as an eco-conscious alternative that supports the principles of recycling and resource efficiency.
In conclusion, 3D sand printing casting is poised to transform the foundry industry. Its ability to produce complex shapes, reduce lead times, lower costs, and minimal environmental impact makes it a highly attractive option for modern manufacturers. As the technology continues to evolve and mature, it is likely to gain further traction, ultimately redefining the standards of precision casting and paving the way for innovations across various sectors. Embracing this technology could be the key to unlocking new possibilities and efficiencies in manufacturing, heralding a new era of production capabilities.
Post time:ነሐሴ . 30, 2024 20:27
Next:can i sand resin