The Art of 3D Sand Casting
3D sand casting is an innovative manufacturing process that combines traditional foundry techniques with cutting-edge 3D printing technology. This method has revolutionized the way metal components are produced, offering enhanced design flexibility, reduced lead times, and cost-effective solutions for various industries. In this article, we'll delve into the basics of 3D sand casting, its applications, benefits, and future prospects.
At its core, 3D sand casting involves creating a mold using a 3D printer, which utilizes a specialized sand mixture that is bound together with a polymer. The process begins with a digital model of the desired part, designed using computer-aided design (CAD) software. This model is then sliced into layers, and a printer constructs the mold layer by layer. The resulting mold cavity precisely mirrors the original design, allowing for intricate details and complex geometries that would be difficult to achieve with traditional sand casting methods.
The Art of 3D Sand Casting
Another significant benefit of 3D sand casting is the ability to produce complex shapes without the need for complicated tooling. Traditional methods often rely on specific patterns and cores to create certain features, which can add to production costs and complexity. In contrast, 3D sand casting allows for the generation of geometrically complex designs directly from the digital file, eliminating the need for multiple patterns and reducing the overall cost per part.
3d sand casting
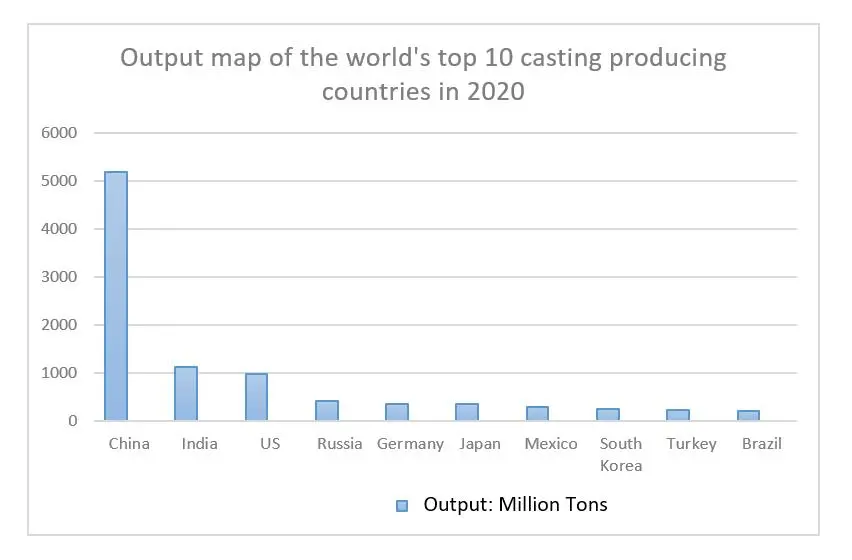
Additionally, the use of sand as a molding material in this process is environmentally friendly. It allows for the recycling of sand, as spent molds can be reused in subsequent production cycles. This sustainable aspect is increasingly important to manufacturers seeking to reduce their environmental footprint and comply with stricter regulations.
The applications of 3D sand casting are vast and varied. Industries that require high-performance components, such as aerospace and automotive, are leveraging this technology to create lightweight and intricate parts that enhance performance and efficiency. Moreover, custom and low-volume production runs are ideal candidates for 3D sand casting, as it eliminates the need for large-scale manufacturing setups.
Looking ahead, the future of 3D sand casting appears promising. As technology continues to advance, we can expect further improvements in printing speed, material properties, and surface finishing, resulting in even higher quality castings. Moreover, the integration of artificial intelligence and machine learning in the design and production processes will likely lead to optimized designs and further cost reductions.
In conclusion, 3D sand casting stands at the intersection of technology and traditional manufacturing, offering numerous advantages that cater to modern industrial demands. As the industry continues to evolve, this innovative process will play a critical role in shaping the future of metal casting, paving the way for more efficient, sustainable, and adaptable manufacturing practices.
Post time:መስከ . 01, 2024 07:03
Next:Iron Sand Casting | Precision Metal Casting Solutions