High Volume Sand Casting An Efficient Solution for Mass Production
Sand casting is one of the oldest and most widely used methods of metal casting. It involves creating a mold from fine sand, which is then used to pour molten metal and produce a wide range of components. When it comes to high volume sand casting, the benefits of this technique are magnified, providing manufacturers with an efficient and cost-effective solution for large-scale production.
High volume sand casting is particularly advantageous for industries that require large quantities of standardized components. These might include the automotive, aerospace, and consumer goods sectors. The process can produce parts in the thousands, making it ideal for mass production runs without sacrificing quality or precision.
One of the foremost advantages of high volume sand casting is its flexibility in design. Complex shapes can be easily created using sand as the medium, allowing for intricate designs that might be impossible with other methods. This is particularly useful for industries requiring bespoke components that fit specific functions or designs. The ability to create precision parts reduces the need for secondary operations, such as machining, often lowering overall manufacturing costs.
The scalability of high volume sand casting is another factor that drives its popularity. Once the initial setup and mold creation are complete, the process can produce numerous casts in a short amount of time. Automated machinery can further enhance this volume, allowing manufacturers to ramp up production without a significant increase in labor costs or time. Automation also plays a critical role in ensuring repeatability and consistency across all produced components.
high volume sand casting
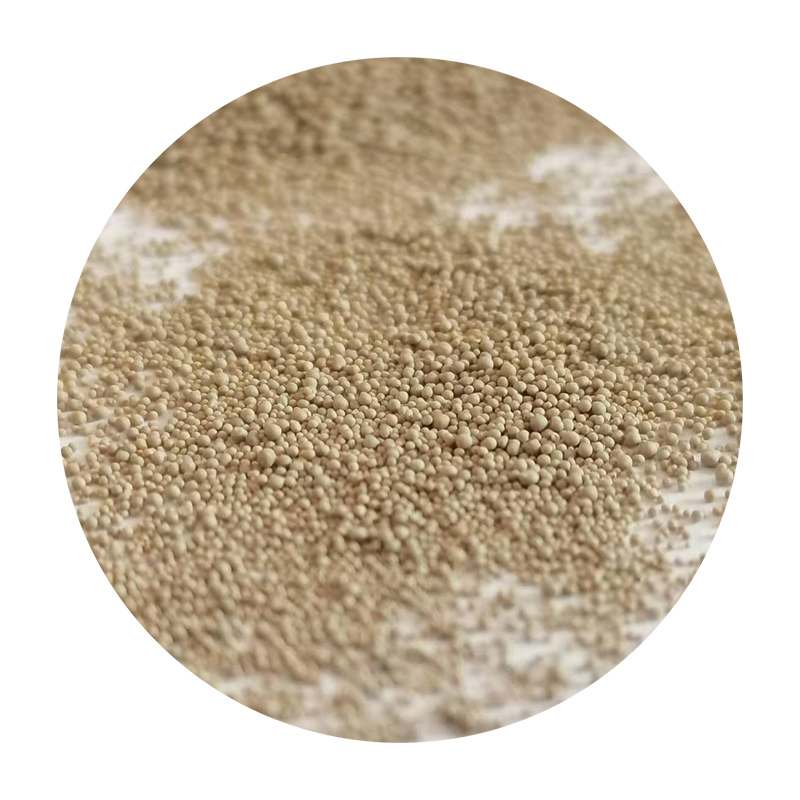
Moreover, the materials used in sand casting are generally less expensive than those required for other casting methods. Silica sand, binders, and coatings can be sourced at a low cost, making the initial investment more appealing for companies looking to minimize expenses. The melting point of metals used in sand casting, such as aluminum and iron, is also manageable, facilitating a higher output rate.
Environmental considerations are becoming increasingly important in manufacturing processes, and high volume sand casting is no exception. Modern techniques focus on reducing waste, recycling sand, and minimizing energy consumption. Many manufacturers now emphasize the use of eco-friendly binders and sustainable practices, ensuring that high-volume production aligns with global sustainability goals.
However, it’s essential to acknowledge some limitations of high volume sand casting. The surface finish of sand cast products may not match that of other casting techniques, such as investment casting. This is often due to the rough texture of sand molds. Additionally, while the flexibility of design is a significant advantage, certain intricate features may be challenging to achieve compared to more specialized casting methods.
Quality control measures are also critical in high volume sand casting. As production rates increase, it becomes paramount for manufacturers to implement rigorous testing and inspection protocols. Advanced technologies, such as computer simulations and digital monitoring, can help detect potential defects early in the process, ensuring that the final products meet required specifications and standards.
In conclusion, high volume sand casting stands out as a highly efficient method for mass-producing metal components in various industries. With its cost-effectiveness, flexibility in design, and scalability, it remains a go-to solution for manufacturers seeking to optimize their production processes. As technology continues to advance, the potential for high volume sand casting is likely to expand, allowing for even greater innovations and applications in the future. Embracing this age-old technique remains a testament to the ingenuity and resourcefulness of modern manufacturing practices.
Post time:Des . 19, 2024 12:04
Next:how accurate is sand casting