When it comes to the foundry industry, the choice of sand plays a crucial role in determining the quality and characteristics of the casting process. Different types of foundry sand are utilized, each with its distinct properties suited for specific applications. This article will explore the various types of foundry sand, their characteristics, and their typical uses.
1. Silica Sand Silica sand is the most commonly used foundry sand. It is primarily composed of silicon dioxide (SiO2) and is known for its high melting point, excellent thermal stability, and durability. Silica sand is predominantly used in the production of ferrous (iron and steel) and non-ferrous (aluminum) castings. Its granule size can be adjusted to improve the quality of molds and cores, allowing for better detail reproduction in the final casting.
When it comes to the foundry industry, the choice of sand plays a crucial role in determining the quality and characteristics of the casting process. Different types of foundry sand are utilized, each with its distinct properties suited for specific applications. This article will explore the various types of foundry sand, their characteristics, and their typical uses.
3. Resin-Bonded Sand Resin-bonded sands are produced by mixing silica sand with a thermosetting resin binder. This type of sand offers several advantages, including increased strength, better surface finish, and improved dimensional stability when compared to traditional green sand. Resin-bonded sand allows for more complex molds and finer details and is often used in the production of intricate castings in industries such as aerospace and automotive.
different types of foundry sand
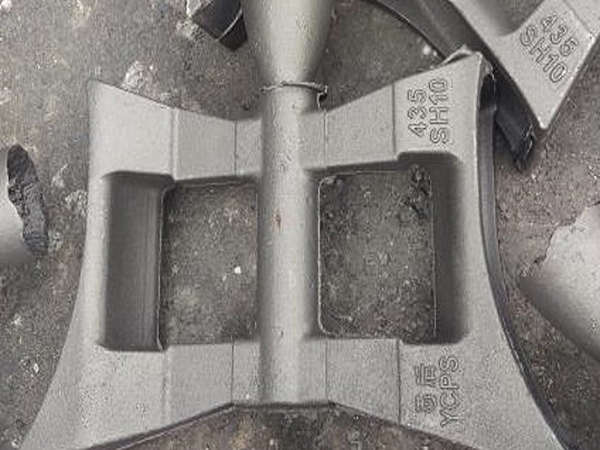
4. No-Bake Sand No-bake sand is similar to resin-bonded sand but does not require any moisture for the molding process. Instead, it utilizes a chemical binder that hardens when exposed to a catalyst. This type of sand is known for its excellent dimensional accuracy and surface finish. It is frequently used in applications that require complex geometries or when rapid mold production is needed.
5. Lost Foam Sand Lost foam casting involves the use of a foam pattern that is coated with sand and then removed by vaporization during the casting process. This technique allows for intricate designs and complex shapes without the need for traditional mold-making methods. The sand used is typically a fine sand mixture, which helps to achieve a smooth and detailed surface finish on the final product.
In conclusion, the choice of foundry sand significantly influences the success of the casting process. Each type of sand has its strengths and specific applications. By understanding the different types of foundry sand—silica sand, green sand, resin-bonded sand, no-bake sand, and lost foam sand—foundries can optimize their operations and enhance the quality of their castings. As technology advances, the development of new sand materials and mixtures continues to evolve, leading to further improvements in the foundry industry.
Post time:Okt . 30, 2024 11:22
Next:sand foundry process